XUE Yonggang, GAO Jinbao, LIU Yicen, FANG Yunchao, LI Yan. Modified Seafoam Fibers for Improving Fire Performance of Non-Intumescent Fire Coatings[J]. Journal of the Chinese Ceramic Society, 2025, 53(3): 666

Search by keywords or author
- Journal of the Chinese Ceramic Society
- Vol. 53, Issue 3, 666 (2025)
Abstract
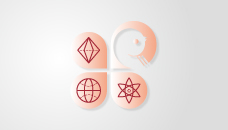
Set citation alerts for the article
Please enter your email address