Wei ZHANG, Zong-wang HAN, Xiang CHENG, Wei-bin RONG, Hong-yu ZHENG. Research on straightness error measurement of part axis based on machine vision[J]. Optics and Precision Engineering, 2021, 29(9): 2168

Search by keywords or author
- Optics and Precision Engineering
- Vol. 29, Issue 9, 2168 (2021)
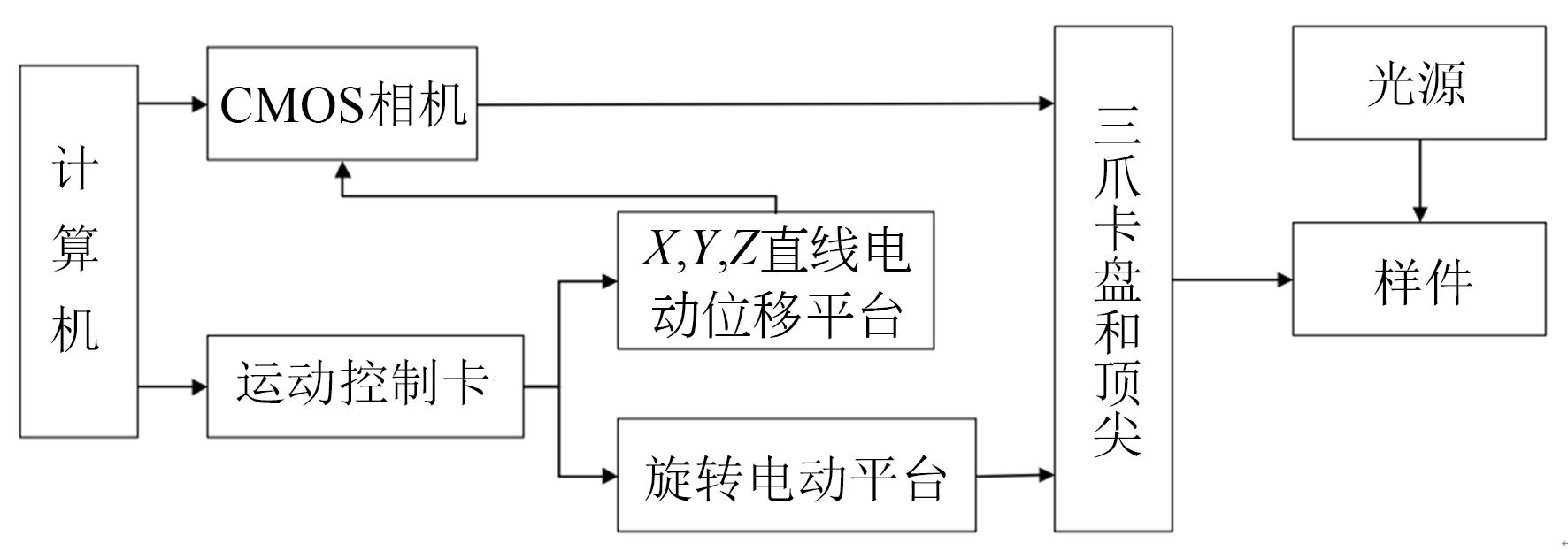
Fig. 1. Schematic diagram of straightness measurement system

Fig. 2. Structure of straightness measurement platform

Fig. 3. Flow chart of straightness error detection

Fig. 4. Schematic of calculating pixel coordinates of central axis

Fig. 5. Schematic of binary coded double tangency points crossover operation

Fig. 6. Schematic of minimum area condition

Fig. 7. Flow chart of big variation with two tangent points

Fig. 8. Straightness measuring platform

Fig. 9. Evaluation function in this paper

Fig. 10. Graphical user interface

Fig. 11. Image after image processing

Fig. 12. Graph of central axis fitting

Fig. 13. Partial enlarged detail of part central axis

Fig. 14. Iteration graph of genetic algorithm by big mutation and double tangent points crossover

Fig. 15. Measurement results of straightness error

Fig. 16. Iteration results of straightness error
|
Table 1. Specification of each motion stages
|
Table 2. Straightness error evaluation results
|
Table 3. Comparison of straightness error results
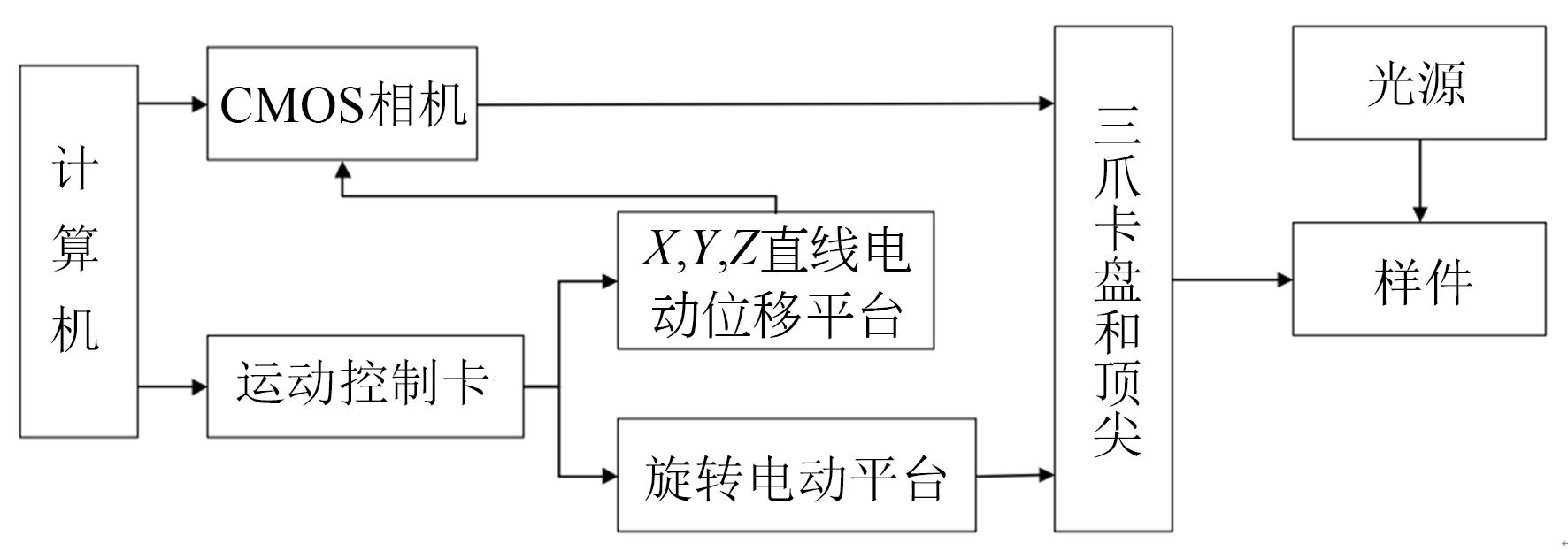
Set citation alerts for the article
Please enter your email address