Shichong Fu, Dan Zhang, Qun Luo. Leakage Identification and Localization Method for Gas Transmission Pipeline Based on Distributed Acoustic Sensing[J]. Laser & Optoelectronics Progress, 2025, 62(3): 0306003

Search by keywords or author
- Laser & Optoelectronics Progress
- Vol. 62, Issue 3, 0306003 (2025)
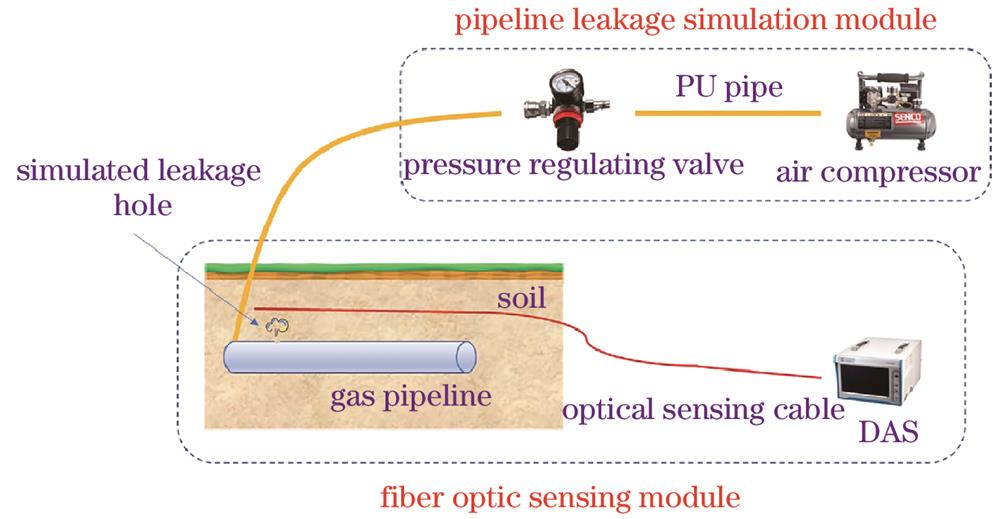
Fig. 1. Schematic diagram of the gas leakage simulation
![Schematic diagram of the optical sensing cable with a spiral structure[20]](/richHtml/lop/2025/62/3/0306003/img_02.jpg)
Fig. 2. Schematic diagram of the optical sensing cable with a spiral structure[20]

Fig. 3. Image of pipeline leakage hole

Fig. 4. Relative position diagram of optical sensing cable and pipeline

Fig. 5. Time-domain intensity change curves of the sensing channel near the leak point

Fig. 6. Time-domain intensity change curves of background noise and leakage signal

Fig. 7. Comparison of frequency spectra between leakage signal and background noise

Fig. 8. STFT results of background noise and leakage signal (0‒15 s is background noise, 15‒30 s is leakage signal)

Fig. 9. Comparison of frequency spectra between background noise and leakage signal when leakage distance is 12 cm

Fig. 10. STFT result of time-averaged DAS signal

Fig. 11. Schematic diagram of leakage location in gas transmission pipeline

Fig. 12. Spectral average amplitude distribution of each sensing channel

Fig. 13. Comparison of spectra between the 6th sensing channel and the 8th sensing channel

Fig. 14. Distribution of correlation coefficient between the 6th sensing channel and the 8th sensing channel

Fig. 15. Cross-correlation result between the 6th sensing channel and the 8th sensing channel
|
Table 1. Results of leakage precision location
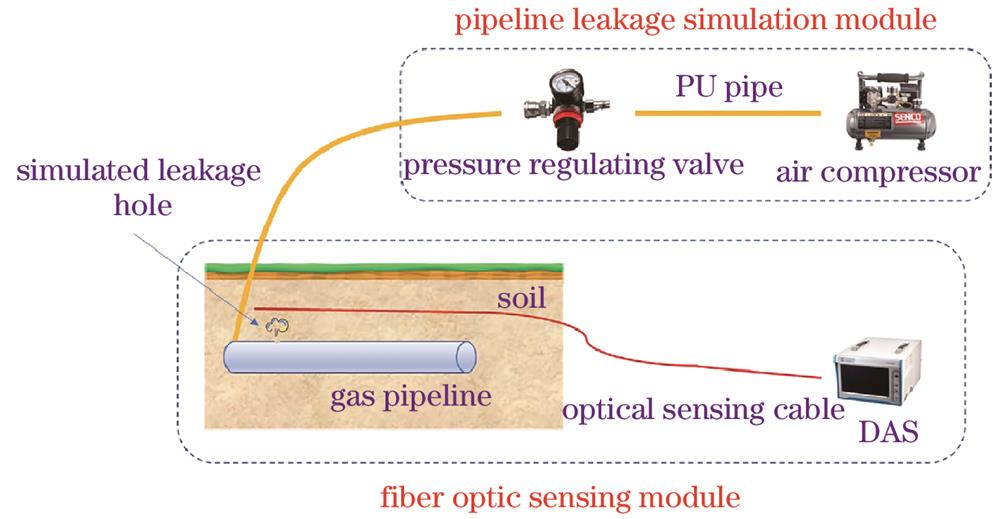
Set citation alerts for the article
Please enter your email address