WANG Xiao, ZHANG Di, GU Chun-xing, SHEN Zong-bao, LIU Hui-xia. Large area micro bending method by soft punch under laser shock wave based on multi-groove mold[J]. Optics and Precision Engineering, 2014, 22(9): 2292

Search by keywords or author
- Optics and Precision Engineering
- Vol. 22, Issue 9, 2292 (2014)
Abstract
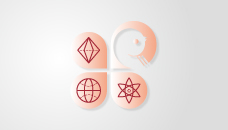
Set citation alerts for the article
Please enter your email address