Weiyi Yuan, Min Fu, Zhixian Li, Zefeng Wang, Zilun Chen. 2 kW Bidirectional Fiber Cladding Power Stripper[J]. Laser & Optoelectronics Progress, 2023, 60(17): 1714003

Search by keywords or author
- Laser & Optoelectronics Progress
- Vol. 60, Issue 17, 1714003 (2023)
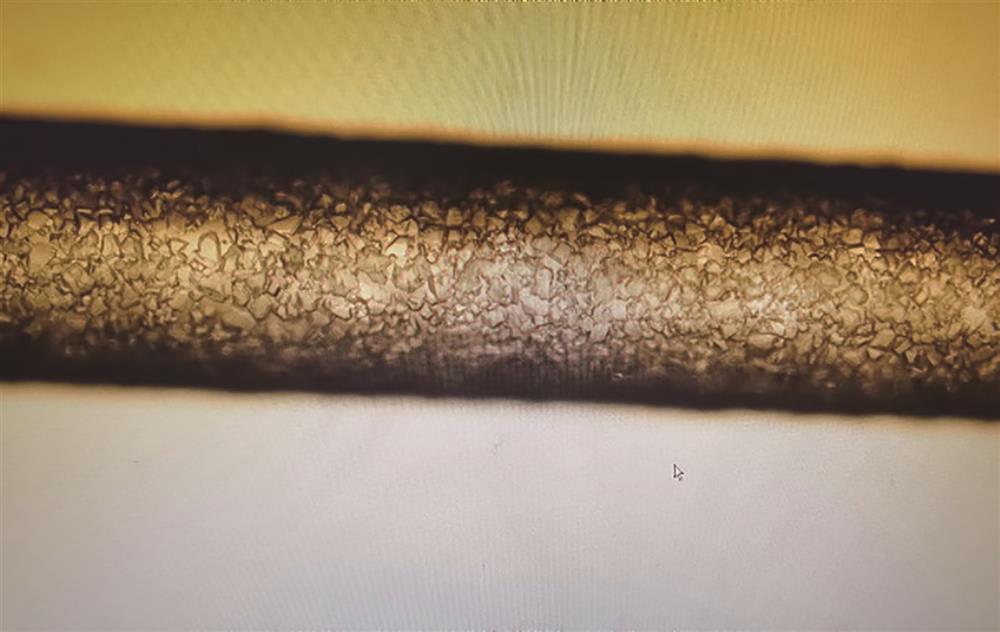
Fig. 1. Surface of corroded optical fiber
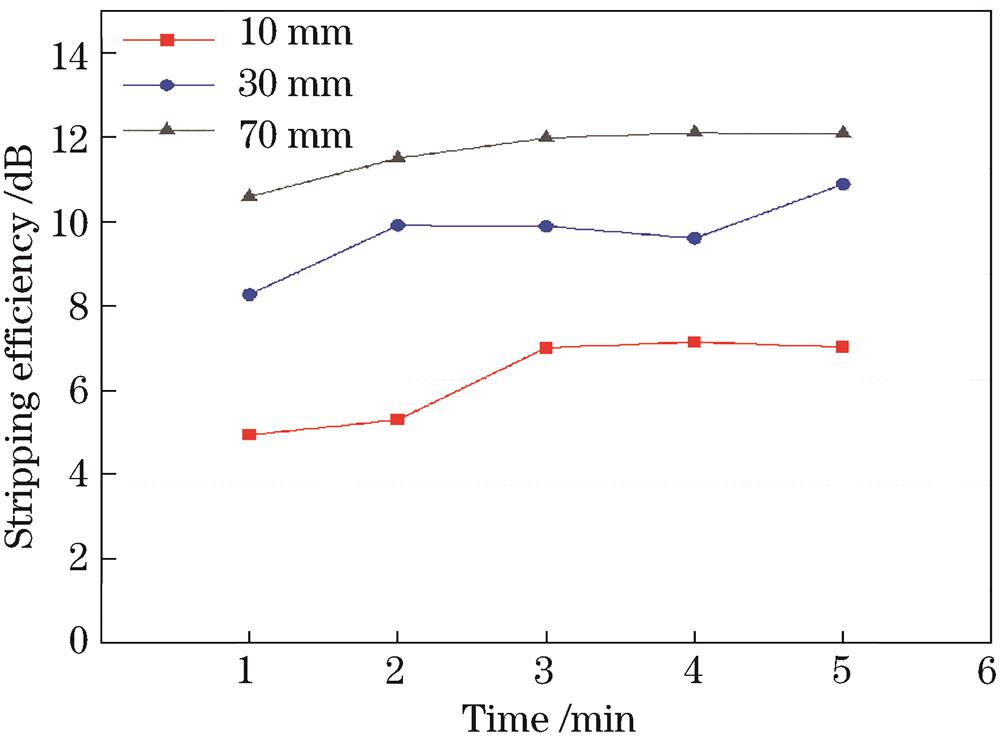
Fig. 2. Relationship between stripping efficiency and corrosion time under different corrosion lengths

Fig. 3. Corroded optical fiber

Fig. 4. Temperature of CPS#1 with 600 W input power

Fig. 5. Stripping efficiency and temperature test optical path diagram of CPS#1

Fig. 6. CPS#1 output power, temperature, and stripping efficiency varying with input power

Fig. 7. Temperature of CPS#1 with 2 kW input power

Fig. 8. CPS#1 temperature with reverse input light

Fig. 9. Schematic of bidirectional designed CPS

Fig. 10. Variation of output power with input power for bidirectional optical input

Fig. 11. CPS#2 temperature with forward input

Fig. 12. CPS#2 temperature with reverse input

Fig. 13. Physical drawing of CPS sleeve glass tube

Fig. 14. Schematic of water cooling fixture

Fig. 15. Cross-section drawing of water cooling fixture

Fig. 16. Physical drawing of water cooling fixture
|
Table 1. CPS#1 preparation process
|
Table 2. CPS#2 preparation process
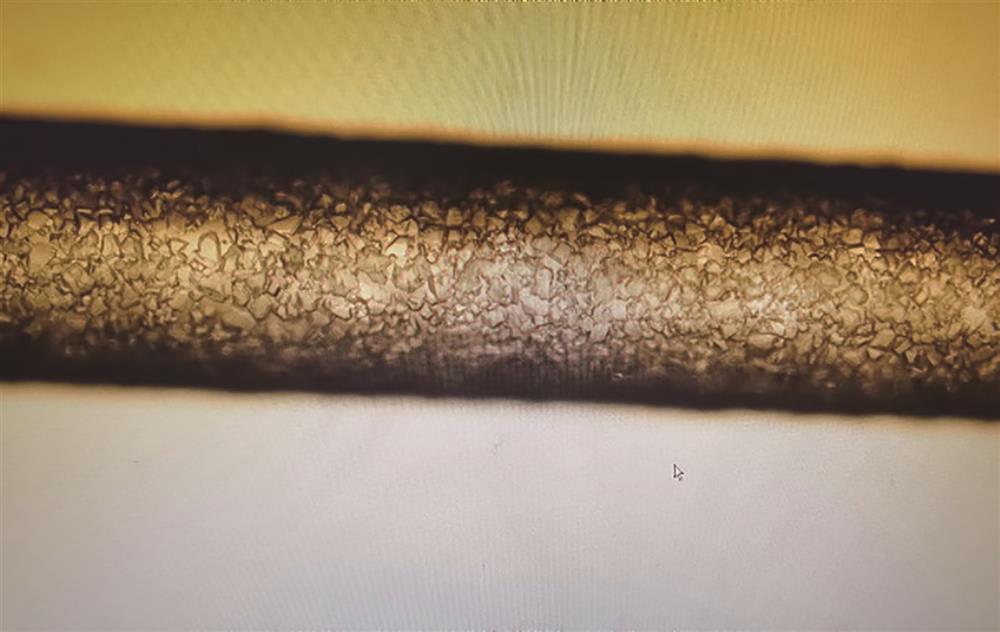
Set citation alerts for the article
Please enter your email address