Jian Yuan, Lei Zhang. Novel Design of Athermal and Rigid Support Structure for Small- and Medium-Aperture Mirrors[J]. Laser & Optoelectronics Progress, 2024, 61(5): 0522005

Search by keywords or author
- Laser & Optoelectronics Progress
- Vol. 61, Issue 5, 0522005 (2024)

Fig. 1. Optical path of the off-axis three mirror anastigmat camera
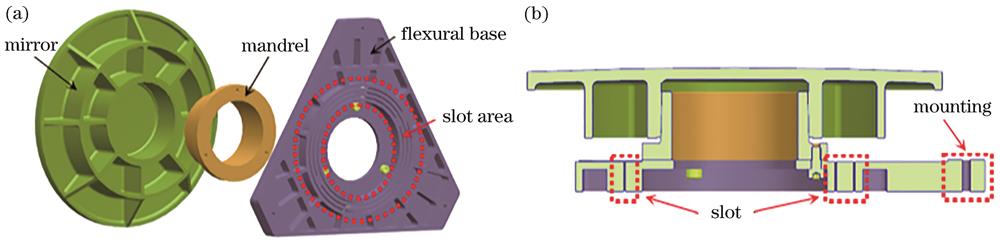
Fig. 2. Secondary mirror with conventional flexural support. (a) Internal components; (b) assembling relationship

Fig. 3. Details of rigid support structure

Fig. 4. Athermal principle of rigid support

Fig. 5. FEA model of secondary mirror assembly

Fig. 6. Deformation nephogram under temperature rise loadcase. (a) Novel rigid support; (b) flexural support

Fig. 7. Surface accuracy test of secondary mirror. (a) Testing optical path; (b) layout of test site; (c) interferogram

Fig. 8. Vibration test for secondary mirror assembly. (a) Test site; (b) data of sweep test along X direction

Fig. 9. Simulated assembling tolerance test of secondary mirror
|
Table 1. Design requirements for secondary mirror assembly
|
Table 2. Material properties of secondary mirror assembly
|
Table 3. Simulation results under main loadcases
|
Table 4. Modal analysis results of secondary mirror assembly
|
Table 5. Comparison of working characteristics between two support structures
|
Table 6. Test results of surface accuracy at different stages

Set citation alerts for the article
Please enter your email address