Wangqi Fu, Bo Qian, Zhiyuan Liu, Bo Li. Structure and Properties of 316L Stainless Steel Lattice Reinforced via Selective Laser Melting Using Vanadium Carbide Particles[J]. Laser & Optoelectronics Progress, 2019, 56(24): 241401

Search by keywords or author
- Laser & Optoelectronics Progress
- Vol. 56, Issue 24, 241401 (2019)

Fig. 1. Powder morphologies before and after ball milling. (a) 316L stainless steel powder; (b) V8C7/316L composite powder; (c) partial enlargement of composite powder
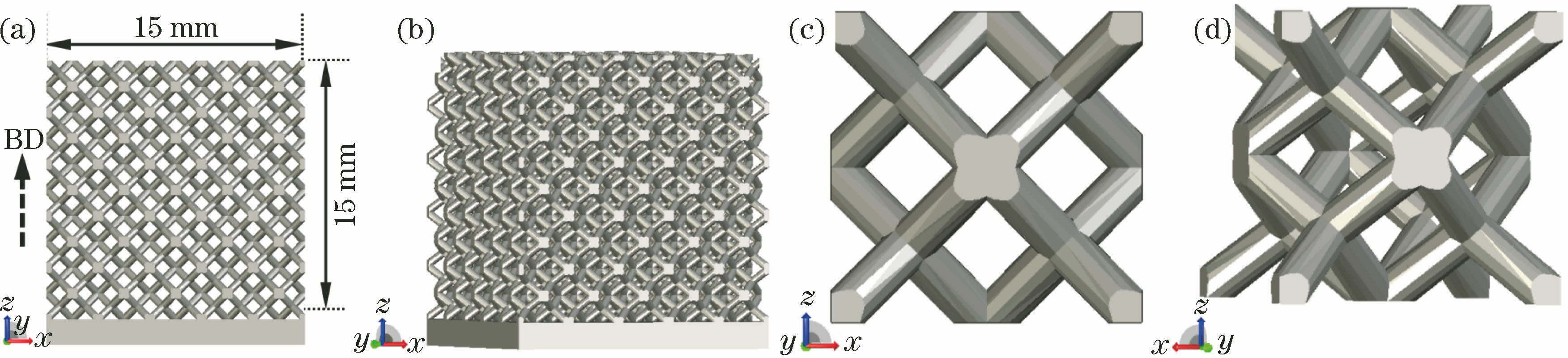
Fig. 2. Diagrams of lattice structure. (a) Front view of lattice structure; (b) oblique view of lattice structure; (c) front view of unit cell; (d) oblique view of unit cell

Fig. 3. Comparison of density of V8C7/316L MMCs under different process parameters

Fig. 4. Microstructures of samples in building direction. (a) Sample of 316L stainless steel; (b) sample of V8C7/316L composite

Fig. 5. SEM image of V8C7/316L composite. (a) Microstructure; (b) partial enlargement of Fig. 5 (a); (c) grain boundaries and reinforcements

Fig. 6. XRD pattern of V8C7/316L composite

Fig. 7. Schematics of formation mechanism of microstructural characteristics. (a) 316L stainless steel; (b) V8C7/316L composite

Fig. 8. Stress-strain curves of 316L and V8C7/316L samples. (a) Stress-strain curves under tension, (b) stress-strain curves under compression

Fig. 9. Morphologies of V8C7/316L lattice structure. (a) Macroscopic morphology; (b) SEM image of upper surface; (c) SEM image of overhanging structure in lattice

Fig. 10. Compressive properties of 316L and V8C7/316L lattice structures. (a) Stress-strain curves; (b) partial enlarged view of stress-strain curves; (c) compression deformation behavior
|
Table 1. Chemical composition of 316L stainless steel powder
|
Table 2. Physical characteristics of V8C7 powders

Set citation alerts for the article
Please enter your email address