Zhaoyao Shi, Yiming Fang, Xiaoyi Wang. Research Progress in Gear Machine Vision Inspection Instrument and Technology[J]. Laser & Optoelectronics Progress, 2022, 59(14): 1415006

Search by keywords or author
- Laser & Optoelectronics Progress
- Vol. 59, Issue 14, 1415006 (2022)
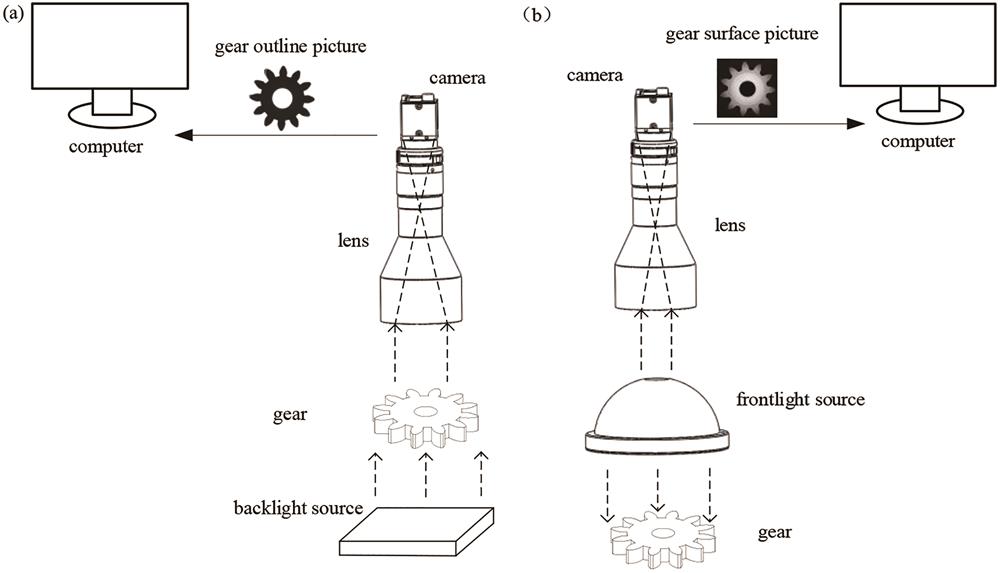
Fig. 1. Composition of the gear visual inspection instrument. (a) Gear accuracy measuring system; (b) gear defect inspection system
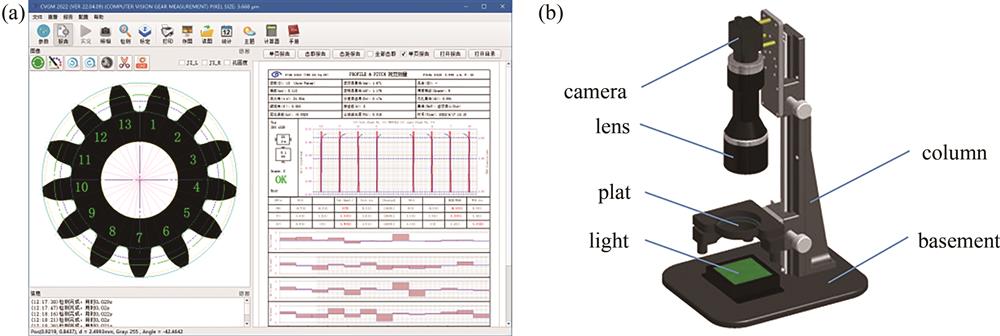
Fig. 2. CVGM fine module gear measuring system. (a) CVGM software; (b) CVGM instrument

Fig. 3. Gear integrated error analysis based on vision measurement
![Conveyor belt gear visual inspection system[12]](/Images/icon/loading.gif)
Fig. 4. Conveyor belt gear visual inspection system[12]

Fig. 5. Gear visual inspection equipment using manipulator and automatic device
![Gear visual inspection and sorting system with glass turntable[13]](/Images/icon/loading.gif)
Fig. 6. Gear visual inspection and sorting system with glass turntable[13]

Fig. 7. Software interface of on-line inspection and sorting system for injection molded plastic gears

Fig. 8. Tooth profile extraction based on Canny operator

Fig. 9. Sub-pixel edge processing
![Gear defect feature extraction and pattern recognition[36]](/Images/icon/loading.gif)
Fig. 10. Gear defect feature extraction and pattern recognition[36]

Fig. 11. Integrated error curve of bidirectional section obtained by CVGM

Fig. 12. Calibration of image acquisition system and “virtual gear artifact” of CVGM. (a) Calibration piece; (b) virtual gear template

Fig. 13. Types of gear defects
|
Table 1. Performance comparison of classical differential operators in gear edge detection
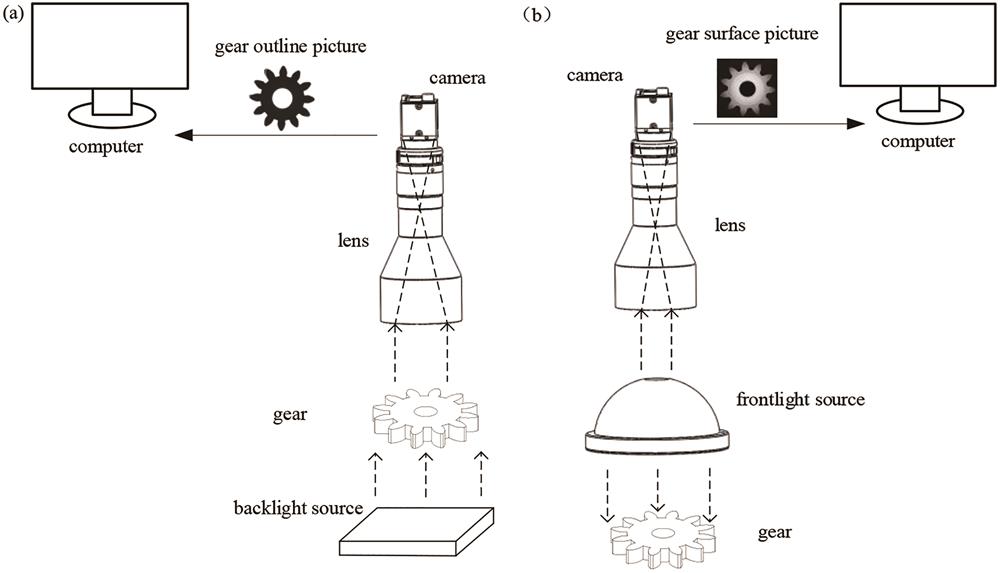
Set citation alerts for the article
Please enter your email address