LI Xiao-zhou, YU Hua-dong, XU Jin-kai, LI Yi-quan, ZHAO Ping. Theory and experiments of cutting forces in micro-cutting process[J]. Optics and Precision Engineering, 2009, 17(5): 1086

Search by keywords or author
- Optics and Precision Engineering
- Vol. 17, Issue 5, 1086 (2009)
Abstract
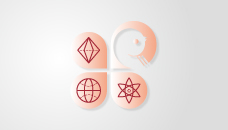
Set citation alerts for the article
Please enter your email address