Wenxi Yu, Guili Xu. Connector Surface Crack Detection Method[J]. Laser & Optoelectronics Progress, 2022, 59(14): 1415015

Search by keywords or author
- Laser & Optoelectronics Progress
- Vol. 59, Issue 14, 1415015 (2022)
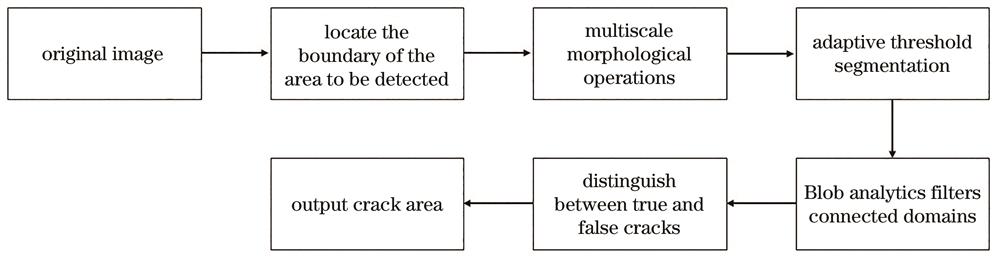
Fig. 1. Flow chart of the designed method

Fig. 2. Original image

Fig. 3. Result of image binarization processing. (a) Image to be processed; (b) result of binarization processing

Fig. 4. Boundary detection result. (a) Image of the area to be detected; (b) masked image of the area to be detected

Fig. 5. 12 structural elements constructed in this paper

Fig. 6. Comparison of extraction effect between the proposed method and black hat operation. (a) Black hat operation; (b) proposed method

Fig. 7. Columnwise projection result

Fig. 8. Image segmentation result

Fig. 9. Schematic of location features

Fig. 10. Schematic of spindle direction

Fig. 11. Schematic of the equivalent ellipse of the cracked area

Fig. 12. Detection result of Blob analysis

Fig. 13. Some pseudo cracks and detection results. (a) Pseudo-crack original images; (b) test results

Fig. 14. Physical picture of crack detection system

Fig. 15. Detection result comparison of different methods
|
Table 1. Detection results
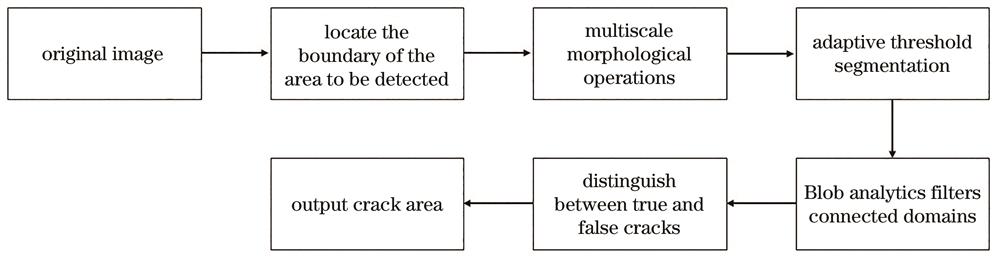
Set citation alerts for the article
Please enter your email address