RONG Zhidan, CHEN Hao, GAO Yun, OUYANG Hanliang. Representative Elementary Size of Mortar’s Mesostructure[J]. Journal of the Chinese Ceramic Society, 2024, 52(11): 3537

Search by keywords or author
- Journal of the Chinese Ceramic Society
- Vol. 52, Issue 11, 3537 (2024)
Abstract
Introduction
As a heterogeneous multiphase material, cement-based material has a significant correlation between its macroscopic properties and microstructure, and exhibits significant scale dependent characteristics. Representative element is defined as the smallest element that can represent the macroscopic property of multi-scale material. It is usually very difficult to study materials at the full scale. Selecting representative element of appropriate size can to some extent represent the overall characteristics, providing possibilities for microscopic calculations. Therefore, the appropriate selection of representative elementary size (RES) is of great significance for further elaborating the structure-performance relationship in micro computational research. For cement mortar, there has been considerable research on the RES of mortar’s microstructure of, but there is a lack of research on the RES of mortar’s mesostructure. Only scholar such as Winslow reported a value of 10–30 mm in early research with relatively single dependent indicator. In view of this, combined with digital image processing and analysis techniques, the statistical characteristics of the spatial distribution of aggregates were calculated from two-dimensional and three-dimensional perspectives by using the average proportion function, two-point correlation function and radial distribution function in this paper. Finally, the representative elementary size of the mortar’s mesostructure was explored.
Methods
Three types of cement mortars blended with cement, fly ash (FA), silica fume (SF) and sand were prepared in this research. The cement used was P·II52.5 in accordance with the relevant Chinese standard. The density of cement and FA are 3.11 g/cm3 and 2.27 g/cm3, respectively. The specific surface area of FA and SF are 420 m2/kg and 22 000 m2/kg, respectively. The fineness modulus of natural sands and manufactured sands are 1.66 and 2.25, respectively. Besides, one kind of polycarboxylic-type high performance water reducer was adopted as the superplasticizer and the water reducing ratio was not less than 40%.The raw materials (cement, fly ash, silica fume, and sand) were mixed uniformly and then the mixed water and additives were added and stirred for 2-3 min until the mixture enters the viscous flow state. Then the uniform mixed slurry was poured at molds and vibrated to enhance compactness. The specimens were demolded after 1 d and then cured in the standard curing room ((20±2) ℃, room humidity >95%). After 28 d of standard curing, the specimens with size of 15 mm×15 mm×15 mm were cut and dried in vacuum at 60 ℃ for 3 d. Afterwards, computed micro-tomography (CT) testing was conducted and 1 000 CT slice images for each specimen were obtained with a resolution ratio of 10 μm.
Results and discussion
After image processing, the influence of noise has been removed and the distribution information of aggregates has been obtained. It can be found that the presentation of natural sand (NS) in CT image is relatively clear and the particle size is relatively uniform, while the shape of manufactured sand (MS) is irregular and the particle size is uneven. Comparing the calculation results of the average volume fraction with the design volume fraction, it can be seen that the former is significantly lower than the latter. The reason is that the composition of the MS is uneven and uneven grayscale values inside may happen due to the crushing process. Therefore, some aggregate information will be lost during the image processing, resulting in a significant deviation between the final result and the design volume fraction. Although the grayscale range of the NS group is very close to that of the cement matrix, its composition is uniform and its shape is regular. After image processing, its distribution information can be retained to a high extent, so the deviation between its calculated volume fraction and the designed volume fraction is very small.As the aggregate fraction increases, there is a significant fluctuation in the RES obtained by calculating the average area fraction on a single CT image, while the average volume fraction obtained by stacking multiple CT images on a three-dimensional structure is equivalent to the average value on a larger area, and the RES results tend to be consistent. The RES is not related to the volume fraction of sand, but is significantly affected by its type. For mortar with natural sand, RES is 2.75–2.90 mm, which is about 9 times of its average particle size. For mortar with manufactured sand, RES is 3.1–3.2 mm, which is about 7 times of its average particle size. Compared with the result mentioned by Winslow that the RES of mortar or concrete is within the range of 10–30 mm, the accuracy of the conclusion in this paper has been improved by one order of magnitude.
Conclusions
The RES of mortar prepared in this paper is not related to the volume fraction of sand, but is significantly affected by its type. For mortar with natural sand, the RES obtained through the average volume proportion function is 2.75 mm, and the RES is 3.1 mm for mortar with manufactured sand. For mortar with natural sand, the RES obtained through two-point probability function and radially distribution function are both 2.9 mm. For mortar with manufactured sand, the RES obtained through two-point probability function and radially distribution function are 3.2 mm and 3.1 mm, respectively.
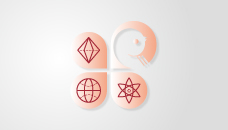
Set citation alerts for the article
Please enter your email address