Haihua Wu, Zhi Liu, Qiang Zhong, Yi Kang, Zenghui Yang, Heng Wei, Jiahuan Hao, Yunxin Ji. Graphite Silicon Carbide Ceramic Composite Made Using Micro-Hot Pressing Additive[J]. Laser & Optoelectronics Progress, 2023, 60(13): 1316023

Search by keywords or author
- Laser & Optoelectronics Progress
- Vol. 60, Issue 13, 1316023 (2023)
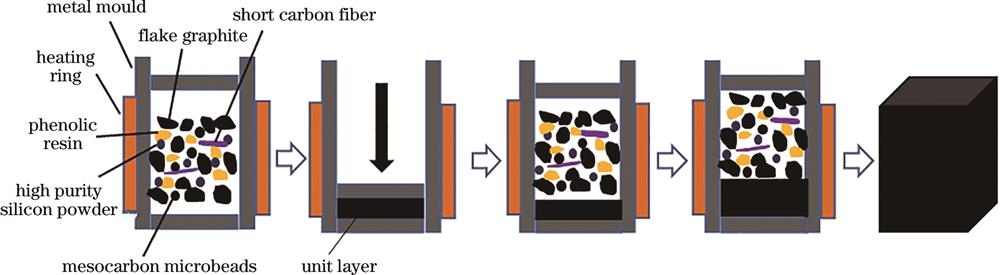
Fig. 1. Process of graphite powder micro-hot pressing additive forming
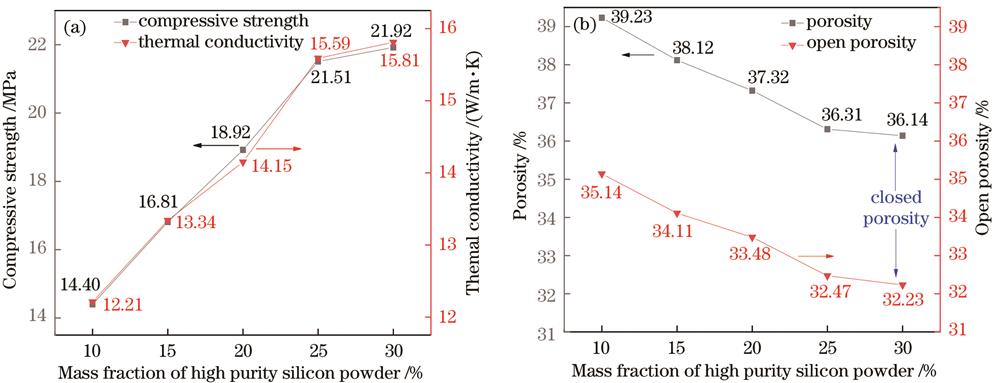
Fig. 2. Effect of the mass fraction of high purity silica powder on the properties of samples. (a) Impact on compressive strength and thermal conductivity; (b) impact on porosity and open porosity

Fig. 3. Morphology of samples sintered at high temperature. (a) a=10%; (b) a=15%; (c) a=20%; (d) a=25%; (e) a=30%

Fig. 4. XRD patterns of samples with different contents of high purity silica powder

Fig. 5. Effect of the mass fraction of cut carbon fiber on the properties of sample. (a) Impact on compressive strength and thermal conductivity; (b) impact on porosity and open porosity

Fig. 6. Morphology of samples sintered at high temperature. (a) b=0%; (b) b=2%; (c) b=4%; (d) b=6%; (e) b=8%

Fig. 7. Effect of the mass fraction of mesophase carbon microspheres on the properties of samples. (a) Impact on compressive strength and thermal conductivity; (b) impact on porosity and open porosity

Fig. 8. TG-DSC curve of mesophase carbon microspheres

Fig. 9. Morphology of sample after sintering. (a) c=0%; (b) c=9%; (c) c=15%; (d) c=21%; (e) c=27%

Fig. 10. Oxidation weight loss curves of two materials at 1200 ℃. (a) Graphite/sic ceramic composite samples; (b) graphite cast material samples
|
Table 1. Comparison of properties of graphite/silicon composites casting materials
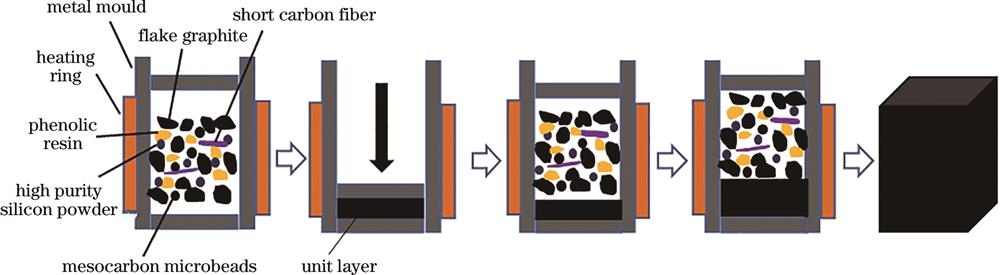
Set citation alerts for the article
Please enter your email address