Ziyong Ma, Fuquan Zhang, Lidong Ma, Hechen Ma, Jiahao Hang. Line-Structured Light Based Micro-Irregular Component Geometric Dimension Measurement Method[J]. Laser & Optoelectronics Progress, 2023, 60(15): 1512001

Search by keywords or author
- Laser & Optoelectronics Progress
- Vol. 60, Issue 15, 1512001 (2023)
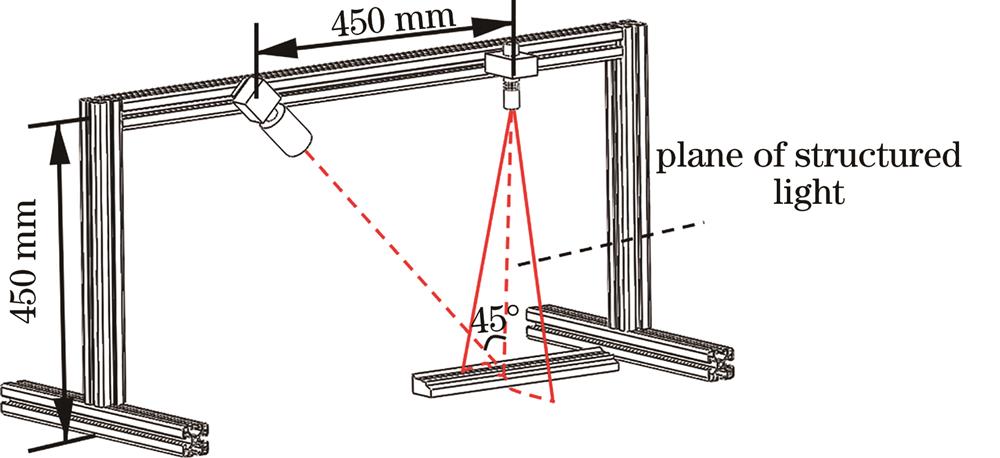
Fig. 1. Composition of the measuring system
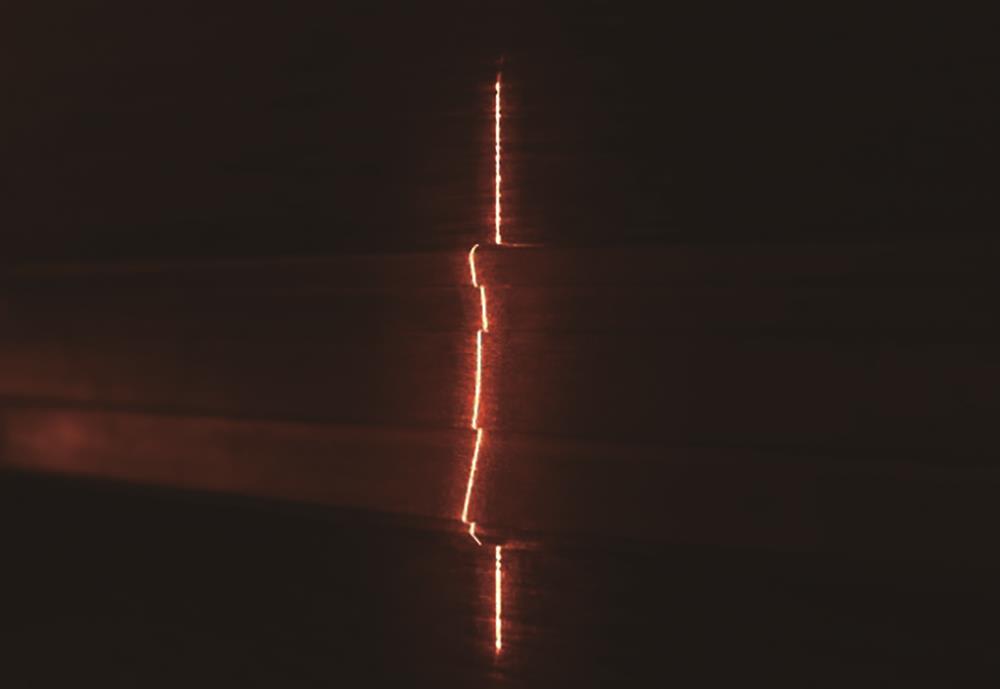
Fig. 2. Image of profile of micro irregular component

Fig. 3. Camera imaging model

Fig. 4. Line-structured light. (a) Original image of line-structured light; (b) Steger thinning image of line-structured light

Fig. 5. Mathematical model of line-structured light

Fig. 6. Selection of central feature points of line-structured light

Fig. 7. Least square fitting plane

Fig. 8. Distance between fitting points and line-structured light plane

Fig. 9. Height measurement of different gauge blocks. (a) Original heights; (b) height measurements; (c) standard deviations of repeated measurement error in height

Fig. 10. Width measurement of different gauge blocks. (a) Original widths; (b) width measurements; (c) standard deviations of repeated measurement error in width

Fig. 11. Measurement test of No. 1 micro irregular component. (a) Original image of the component; (b) position of geometric points; (c) dimension measurement of different parts of the component; (d) geometric dimension error of the component

Fig. 12. Measurement test of No. 2 micro irregular component. (a) Original image of the component; (b) position image of geometric points; (c) dimension measurement of different parts of the component; (d) geometric dimension error of the component

Fig. 13. Measurement test of No. 3 micro irregular component. (a) Original image of the component; (b) position image of geometric points; (c) dimension measurement of different parts of the component; (d) geometric dimension error of the component
|
Table 1. Internal parameters of industrial camera
|
Table 2. Plane equation coefficients of line-structured light
|
Table 3. Fitting accuracy evaluation of line-structured light plane
|
Table 4. Actual thickness value of eleven gauge blocks
|
Table 5. Comparison of maximum measurement error of gauge blocks
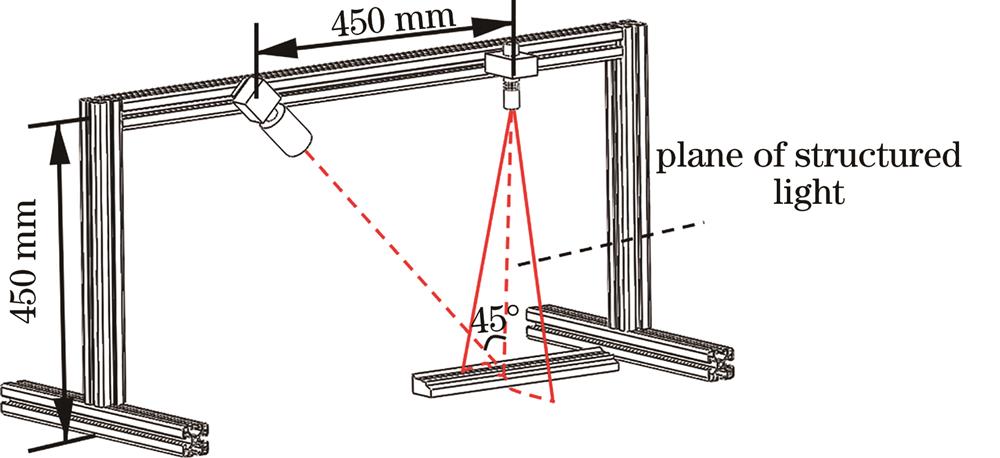
Set citation alerts for the article
Please enter your email address