
- Chinese Optics Letters
- Vol. 22, Issue 10, 100604 (2024)
Abstract
1. Introduction
With the rapid development of atomic clocks, time-frequency has become a current physical quantity with the highest measurement accuracy[1]. High-precision time-frequency signals play an important role in the fields of time-frequency comparison, basic physics research, and space exploration[2–4], and these applications require high-precision time-frequency transfer systems. Current time-frequency transfer systems are mainly based on satellite links[5,6], free-space optical links[7,8] and fiber links[9–11]. Due to the fiber advantages of low loss, strong anti-interference, and abundant resources, time-frequency transfer based on fiber links has become the main means of high-precision time-frequency transfer and has been widely studied. Fiber frequency transfer mainly includes microwave frequency transfer, optical frequency transfer, and optical frequency comb transfer, while microwave frequency transfer has a wide range of application prospects as it can be used directly by electronic devices. In 2018, the University of Western Australia achieved a 160 MHz frequency transfer of
When using fiber links for frequency transfer, the light propagation path in the optical fiber changes due to the influence of external temperature changes. It leads to changes in the optical phase transmitted to the terminals, and thus causes a deterioration in the stability of the transmitted frequency. Therefore, a phase noise compensation device needs to be introduced into the fiber link to compensate for the phase noise due to temperature variations to achieve a high-precision frequency transfer. Traditional phase compensation methods include optical phase compensation and electrical phase compensation. Electrical phase compensation is susceptible to microwave leakage and has poor long-term stability. Optical phase compensation systems are large, small in compensation range, and not easy to industrialize. Therefore, starting from the fiber and finding the optical fiber that is not sensitive to temperature is an important direction for achieving fast, low-cost, and high-precision time-frequency transfer.
As a special fiber that has developed rapidly in recent years, the hollow-core photonic crystal fiber (HC-PCF) has many unique advantages over traditional solid-core fibers, such as low nonlinearity, low propagation delay, and temperature insensitivity[14–17], due to transmission of light in the air core. According to the guiding mechanism, HC-PCF can be divided into the hollow-core photonic bandgap fiber and the hollow-core anti-resonant fiber. In 2015, the University of Southampton proved that the thermal coefficient of delay of the hollow-core photonic bandgap fiber was 2 ps km−1 K−1, which was an order of magnitude lower than that of the traditional solid-core fiber[18]. In 2018, the team proved that zero propagation delay temperature sensitivity could be achieved in a hollow-core photonic bandgap fiber[19]. Therefore, HC-PCF has a bright future in high-precision fiber time-frequency transfer.
Sign up for Chinese Optics Letters TOC. Get the latest issue of Chinese Optics Letters delivered right to you!Sign up now
In this article, we analyze factors that reduce the difficulty of fabrication by theoretically simulating the hollow-core anti-resonant fiber drawing process. The hollow-core anti-resonant fiber with a thicker outer nested tube wall is less sensitive to fluctuations in drawing conditions. By adjusting the wall thickness of the outer nested tube to a thicker value and using its second light conduction band, the difficulty of fabricating kilometer-length, low-loss hollow-core nested anti-resonant nodeless fibers is reduced. The lowest loss of the fabricated fiber is 2.7 dB/km at 1506 nm, and the bandwidth less than 5 dB/km is 1417–1620 nm. With the fiber loop optical-microwave phase discriminator system, we locked the 250 MHz repetition frequency of the optical frequency comb to a rubidium atomic clock. The thermal coefficient of delay for the fabricated hollow-core nested anti-resonant nodeless fiber is measured as 2.7 ps km−1 K−1, which is an order of magnitude lower than the 36.7 ps km−1 K−1 for the conventional single-mode fiber with the same length. We built a high-precision frequency transfer system using the prepared 1050 m hollow-core fiber, and the frequency stability is
2. Method
2.1. Kilometer-scale low-loss hollow-core nested anti-resonant nodeless fiber preparation
Hollow-core nested anti-resonant nodeless fibers (HC-NANFs) are prepared by the traditional two-stage stack-and-draw approach[20]. First, several nested tubes are inserted into a jacketing tube with an outer diameter of 20–30 mm. The capillary tubes are fixed by molds at both ends so that the capillary tubes are closely tangent to the outer jacketing tube and form a preform. The preform is fused and scaled to a cane with an outer diameter of 3–6 mm. Next, the cane is assembled into a drawing tube and air chambers are formed in different areas of cane by specific molds. The stacking process in the first and second stages is completed in a clean room to avoid the contamination of preforms and the fiber breakage in the drawing of the long-distance hollow-core anti-resonant fiber. The hollow-core anti-resonant fibers of specific structures and sizes are drawn through the adjustment of the air pressure in the different air chambers. As the cladding of the hollow-core anti-resonant fiber consists of capillary tubes, the jacketing tubes bear the majority of the tension during the drawing process, and the tensile deformation of the capillary tubes is determined by the evolution of the jacketing tubes. Therefore, we can use the Fitt[21] model to solve for the variation of the jacketing tube throughout the drawing process and use it as the boundary conditions to obtain the variation of the cladding capillary tube dimensions in the axial direction, which has been proved to be feasible in Ref. [22]. We add the cladding capillary tube dynamics equations to the Fitt model and obtain dynamic Eqs. (1)–(4) for hollow-core anti-resonant fiber drawing:
Figure 1.Schematic of the dynamic change of the fiber structure during the HC-NANF drawing.
In the actual drawing process, the gap between the cladding anti-resonant tubes needs to be controlled at a small distance to obtain a low loss, and small inhomogeneities in different anti-resonant tube sizes or positions increase the difficulty of controlling the fiber structure. Therefore, a large drawing tension is often required to control the fiber structure, which often leads to fiber breakage during drawing and thus makes it difficult to fabricate the long-distance hollow-core fiber. Due to the special light-guiding mechanism of the hollow-core anti-resonant fibers, we can choose different tube wall thicknesses and use different anti-resonant light-guiding bands to obtain low loss. We calculated the sensitivity of the nested outer tube wall thicknesses of 450 nm and 1150 nm to the initial preform nested tube size change and air pressure change according to the model we mentioned above. Figure 2(a) calculates the relationship between the fiber nested outer tube size and the preform nested outer tube size for the different wall thickness.
Figure 2.(a) Sensitivity of the fiber nested outer tube size to the preform nested tube size for the different tube thicknesses. (b) Sensitivity of the fiber nested outer tube size to the gas pressure difference for the different tube thicknesses.
In our simulation, the same value is set for each condition of drawing, and the calculated tension is 265 g. We take the preform nested outer tube size of 6.2 mm and fiber nested outer tube size of 24.6 µm as reference. Due to different tube thicknesses, different air pressures need to be set in the calculation to achieve the target fiber nested outer tube size. The preform nested outer tube size is changed and brought into the simulation model to obtain the fiber nested outer tube size. We fitted the results to obtain the sensitivity of the fiber nested outer tube size to the preform nested outer tube size for the wall thickness of 450 nm and 1150 nm as 12.68 µm/mm and 7.0 µm/mm, respectively. The sensitivity of the fiber nested outer tube size to the change in gas pressure is calculated in Fig. 2(b). The pressure difference
We calculated the loss property of the five-ring nested anti-resonant nodeless fibers with different nested outer tube wall thicknesses using COMSOL. The wall thicknesses t1 of the nested inner tubes of the two fibers are both 450 nm. Figure 3 shows the calculated loss spectra, from which it can be seen that the fibers with 1150-nm-wall thickness and 450-nm-wall thickness have almost the same loss of 1 dB/km at 1550 nm. The available bandwidth of the fiber with 1150-nm thickness is 300 nm, which covers the spectral range of the optical frequency comb we use for the frequency transfer. Therefore, we chose 1150 nm as the target nested outer tube thickness to reduce fabrication difficulty, and we successfully prepared the kilometer-long low-loss hollow-core anti-resonant fibers under safe tension.
Sign up for Chinese Optics Letters TOC. Get the latest issue of Chinese Optics Letters delivered right to you!Sign up now
Figure 3.Simulation results of the fiber loss with different nested outer tube thicknesses.
Figure 4(a) shows a scanning electron microscope (SEM) image of the cross section for our fabricated five-ring HC-NANF. The core diameter is 28 µm, and the thicknesses of the outer tube and nested tube are
Figure 4.(a) SEM image of the fabricated HC-NANF. (b) Measured spectral attenuation using the cut-back method. Inset: the near-field camera image of the fabricated fiber output beam. (c) Measurement results of the fabricated fiber length using φ-OTDR.
2.2. Optical frequency comb repetition frequency locking principle
Figure 5 shows a schematic diagram of the fiber loop optical-microwave phase discriminator (FLOM-PD) used to achieve the high-precision locking of the repetition frequency of a mode-locked laser to an atomic clock. A 10 MHz signal from a rubidium atomic clock is multiplied to generate a 1 GHz signal that serves as the microwave signal for the high-speed phase modulator of the FLOM-PD system, which consists of a Sagnac fiber loop, a phase modulator inside the loop, and a non-reciprocal
Figure 5.Schematic diagram of the FLOM-PD principle.
The non-reciprocal
Sign up for Chinese Optics Letters TOC. Get the latest issue of Chinese Optics Letters delivered right to you!Sign up now
2.3. Influence of temperature on optical fiber frequency transfer
The optical fiber is affected by changes in the external environment (temperature, vibration) and propagation delay of light, resulting in the deterioration of the frequency transfer accuracy. In practical applications, the fiber link is inevitably affected by temperature changes in the environment during the day, and it has the greatest impact on the frequency transfer accuracy. Fiber propagation delay
Therefore, the relative frequency change is mainly affected by two factors: the TCD and
Figure 6 shows the effect of the different TCD and temperature variation frequency
Figure 6.Effect of the temperature change on the frequency stability.
2.4. Study on TCD of HC-NANF
After the above analysis of the temperature influence on fiber frequency transfer, we found that the fiber with the smaller TCD is an important direction to achieve a fast, low-cost, and high-precision time-frequency transmission. The TCD of an optical fiber can be expressed as
Figure 7 shows the theoretically calculated TCD curve of the hollow-core fiber used in the experiment and the contribution curves of the longitudinal thermal expansion effect and the thermo-optical effect to the TCD, respectively. It can be seen that most of the light energy is bound in the air core, the thermo-optic effect of silica is neglected in the low-loss bandwidth, and only the longitudinal thermal expansion contributes to the TCD, which is of the magnitude of 2 ps km−1 K−1. It is an order of magnitude lower than that of the conventional solid-core fiber. Therefore, hollow core fibers have potential applications for fast, low-cost, high-precision fiber frequency transfer.
Figure 7.TCD simulation results of the fabricated HC-NANF.
3. Experiment
3.1. Measurement of the hollow-core fiber TCD
Figure 8 is a diagram of the experimental setup for measuring the TCD of the HC-NANF and the single-mode fiber. An optical frequency comb with a repetition frequency of 250 MHz locked on the rubidium atomic clock passes through the 1:9 coupler. One path is detected by the photodetector after passing through 1050 m fabricated HC-NANF placed in the temperature control box, and the other path is detected directly by the photodetector as a reference optical path. The signal frequency detected by the photodetector consists of a repetition frequency of 250 MHz and its octave. In order to better compare the difference between the two paths, we selected a 500 MHz signal as the comparison frequency. In the experiment, we gradually increase the temperature from 0°C to 40°C and use a signal acquisition card to record the voltage change curve, from which we can calculate the change of the phase difference between the two paths with temperature.
Figure 8.Experimental setup for the TCD measurement of the HC-NANF.
Figure 9 shows the experimentally measured change in the phase difference of the two paths with time. It can be seen that when the temperature increases from 0°C to 40°C, the phase difference between the two paths increases from 0.87 rad to 1.22 rad. As the temperature increases, the time delay of the optical frequency comb through the NANF increases and thus results in the phase difference between the two paths of the light changes by 0.35 rad. Using equation
Figure 9.Change of the phase difference between the two paths with time.
3.2. Construction and testing of the frequency transfer system based on the HC-NANF
Figure 10 shows an optical frequency comb transfer system based on the fabricated HC-NANF. The system consists of three parts: frequency locking, frequency transfer, and frequency measurement and evaluation.
Figure 10.Experimental setup of the optical frequency comb transfer system based on the HC-NANF.
A femtosecond mode-locked laser with a repetition frequency of 250 MHz is split into two paths through a fiber coupler. One path passes through the FLOM-PD device to realize the locking of the repetition frequency to the atomic clock, while the other path is used for the frequency transfer. The signal generated by the rubidium atomic clock is multiplied by a frequency multiplier to generate a 1 GHz microwave signal into the FLOM-PD, which completes the phase identification between the optical pulse signal and the microwave signal and passes the error signal to the PZT to control the cavity length of the mode-locked laser. It realizes the locking of the microwave signal of the rubidium atomic clock to the repetition frequency of the optical frequency comb. The optical pulse carrying the microwave reference signal passes through the 1050 m fabricated NANF link for the frequency transfer. The repetition frequency is directly detected by the photodetector and collected by the high-precision frequency counter.
Due to the limitation of the length of the experimental fiber, we set the temperature variation range to 40°C to simulate the long-distance fiber frequency transfer. The 1050 m NANF is put into the temperature control box and the temperature is increased from 0°C to 40°C with a set time of 1 hour and then lowered to 0°C with a set time of 1 hour as well. The time of the periodic temperature change is 2 hours, and the frequency jitter is collected by a frequency counter. As shown in Fig. 11(a), the transmitted optical frequency comb repetition frequency jitter range is 2 mHz during the whole temperature change process. To further evaluate the performance of the frequency transfer system, we use the Allan deviation to characterize the frequency stability. The red curve in Fig. 11(b) shows the stability of the frequency transfer system based on the fabricated NANF, which can reach
Figure 11.(a) Measured repetition frequency jitter of the optical frequency comb. (b) Frequency stability of the 250 MHz frequency transfer system based on the NANF and the SMF.
Based on the experimentally measured TCD values and formula
Figure 12.Simulation results of the changes in the frequency stability of the frequency transfer system based on the NANF and the SMF due to periodic temperature changes.
4. Conclusion
By improving the structural design of the hollow-core anti-resonant fiber, we have reduced the difficulty of preparing long-distance low-loss hollow-core anti-resonant fibers, and successfully fabricated a 1050 m high-performance hollow-core nested anti-resonant nodeless fiber with a minimum loss of 2.7 dB/km at 1506 nm and more than 200 nm bandwidth below 5 dB/km. We investigated the effect of the temperature on the frequency transfer of the fiber links, and theoretically analyzed and calculated thermal sensitivity of the propagation delay of hollow-core anti-resonant fibers. Experimentally, an optical frequency comb with 250 MHz repetition frequency is locked to a rubidium atomic clock by the FLOM-PD system. A high-precision frequency transfer system is accomplished through the fabricated hollow-core fiber, and the frequency stability can reach
References
[15] B. J. Mangan, M. Kuschnerov, J. W. Nicholson et al. First demonstration of hollow-core fiber for intra data center low latency connectivity with a commercial 100 Gb/s interface. Optical Fiber Communications Conference and Exhibition, M3D.4(2015).
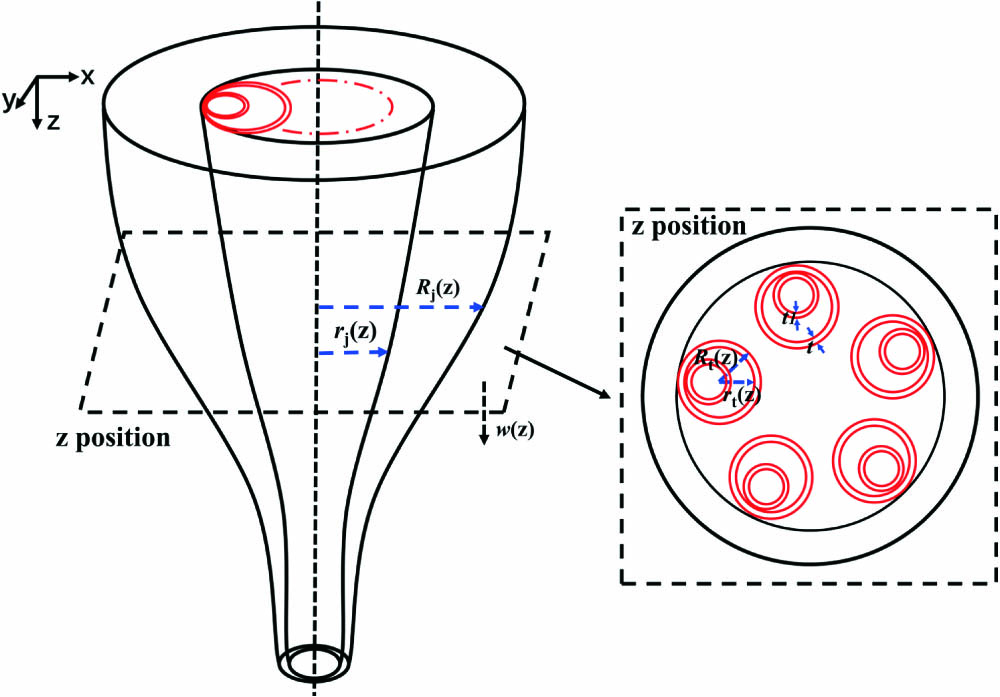
Set citation alerts for the article
Please enter your email address