Ling Ju, Beibei Weng, Xiling Niu, Chuanlu Deng, Yi Huang. Ultrasonic Detection Based on Diaphragm Optical Fiber Fabry-Perot Sensor[J]. Laser & Optoelectronics Progress, 2023, 60(15): 1506002

Search by keywords or author
- Laser & Optoelectronics Progress
- Vol. 60, Issue 15, 1506002 (2023)
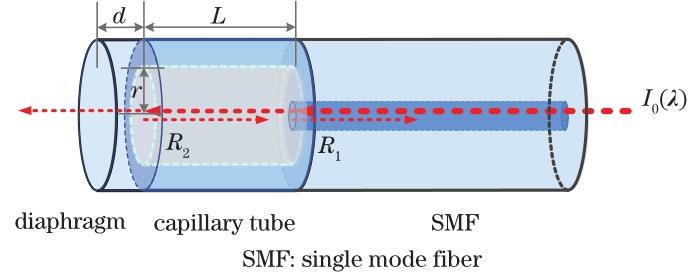
Fig. 1. Schematic diagram of optical fiber Fabry-Perot(F-P) sensor
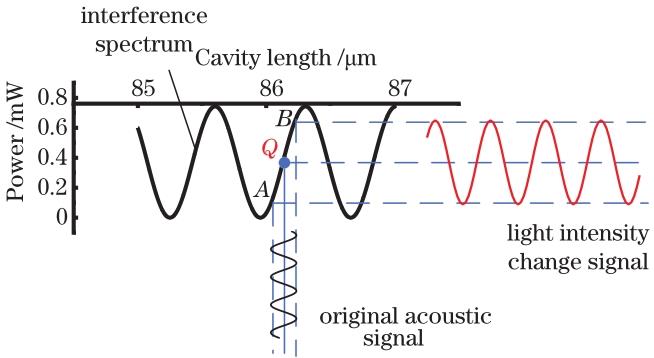
Fig. 2. Sensing mechanism diagram of optical fiber F-P cavity acoustic sensor

Fig. 3. Establishment of simulated acoustic field. (a) 3D simulation model of acoustic field and diaphragm; (b) changes in position of acoustic source relative to diaphragm

Fig. 4. Relation between deformation of diaphragm and distance. (a) Deformation of diaphragm at different distances; (b) relation between maximum deformation of diaphragm and distance

Fig. 5. Relation between deformation of diaphragm and angle. (a) Deformation of diaphragm at different angles; (b) relation between maximum deformation of diaphragm and angle

Fig. 6. Schematic diagram of sensor preparation process. (a) Welding for the first time; (b) cutting for the first time; (c) welding for the second time; (d) cutting for the second time; (e) polishing

Fig. 7. Images of sensor and its spectra before and after polishing. (a) Images of sensor before and after polishing; (b) spectra of sensor before and after polishing

Fig. 8. Schematic diagram of optical fiber F-P ultrasonic sensing system

Fig. 9. Time-domain and frequency-domain signals of 20, 40, and 60 kHz

Fig. 10. Frequency response range of F-P ultrasonic sensor

Fig. 11. Working point position of each sensor sample

Fig. 12. Influence of distance and angle on sensing effect. (a) SNR at different distances; (b) SNR at different angles

Fig. 13. GIS partial discharge simulation device

Fig. 14. Partial discharge detection results of F-P sensor and current transformer (CT). (a) 4.7 kV voltage is applied;(b) 5.1 kV voltage is applied
|
Table 1. Sample parameters
|
Table 2. Comparison of performance indexes of optical fiber acoustic sensor
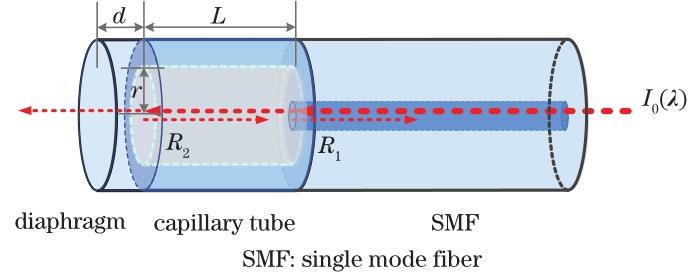
Set citation alerts for the article
Please enter your email address