WANG Bo-wen, WANG Xiao-dong, LI Yun-kai, WAN Li-li, ZHENG Wen-dong, WEI Jia-qi. Magnetostrictive tactile sensor for texture detection[J]. Optics and Precision Engineering, 2018, 26(12): 2991

Search by keywords or author
- Optics and Precision Engineering
- Vol. 26, Issue 12, 2991 (2018)
Abstract
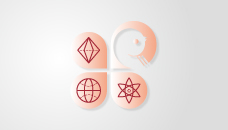
Set citation alerts for the article
Please enter your email address