Bin Zhou, Xiashuang Li, Guifeng Li, Kai Sun, Dongxu Zhang, Yibo Tang. TA1 Surface-Traceable DM Code Marking Based on Low-Power Laser Nitriding[J]. Laser & Optoelectronics Progress, 2025, 62(3): 0314002

Search by keywords or author
- Laser & Optoelectronics Progress
- Vol. 62, Issue 3, 0314002 (2025)
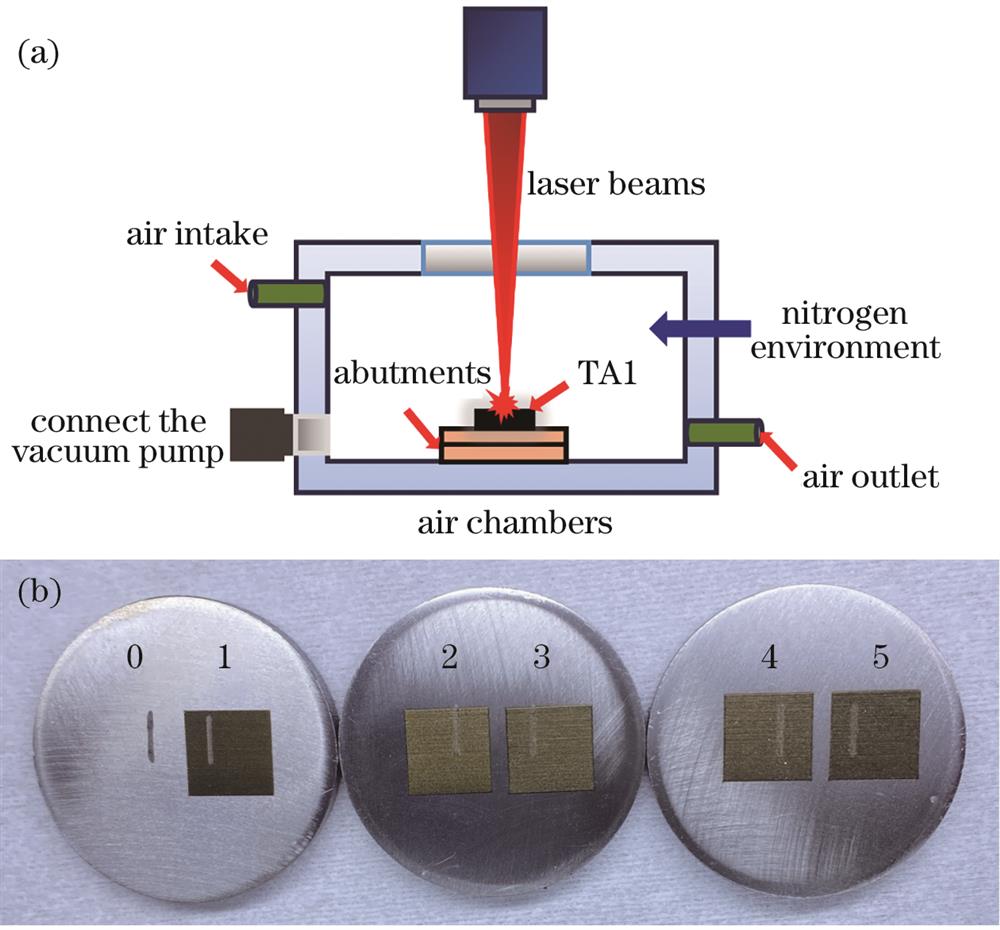
Fig. 1. Laser nitriding device and sample display. (a) Schematic diagram of laser nitriding gas chamber; (b) pure titanium surface laser nitriding sample
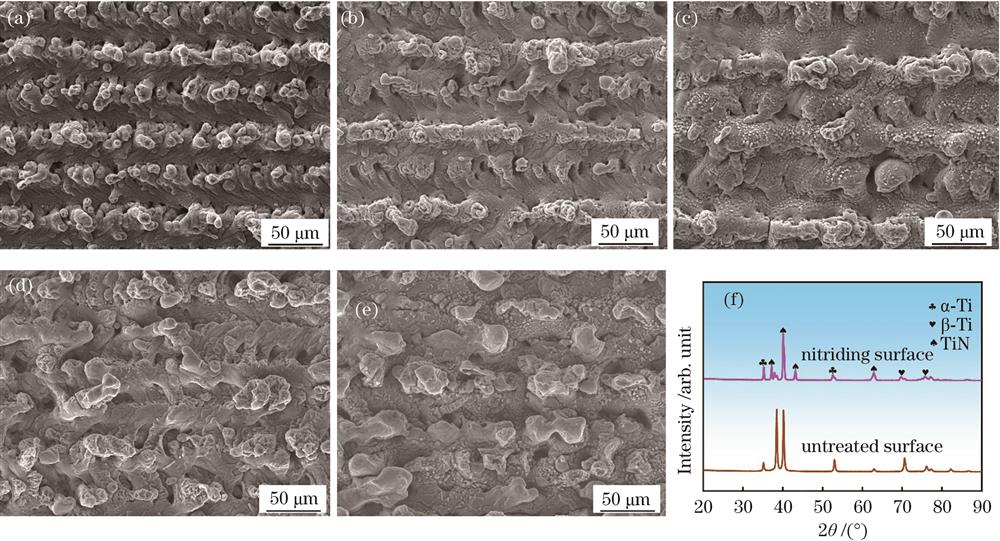
Fig. 2. SEM morphology diagrams of laser nitriding samples. (a) S-1; (b) S-2; (c) S-3; (d) S-4; (e) S-5; (f) XRD results of matrix and S-1

Fig. 3. Cross-sectional morphology of nitride layer and line scan results of N element under different laser process parameters. (a) S-1; (b) S-2; (c) S-3; (d) S-4; (e) S-5

Fig. 4. Nitride layer thickness at different laser powers

Fig. 5. Two-dimensional profile curves of surface hardness and wear marks of each sample. (a) Surface hardness; (b) two-dimensional profile curves of wear marks

Fig. 6. 3D topography of laser nitriding sample after abrasion test. (a) S-0; (b) S-1; (c) S-2; (d) S-3; (e) S-4; (f) S-5

Fig. 7. Image of wear marks and coefficient of friction curves of laser nitriding specimens

Fig. 8. Sample friction coefficient trend and depth and width of wear marks. (a) Trend of friction coefficient of sample; (b) depth and width of wear marks

Fig. 9. (a) Wear volume and (b) wear amount of each sample with loading load of 2 N and loading time of 20 min

Fig. 10. Schematic diagram of QR code calibrator (a) and filling mode inside the DM code module and the"module indentation compensation"(b)

Fig. 11. Boundary diffusion during laser marking and making QR code. (a) Schematic diagram of boundary diffusion; (b) QR code for laser marking

Fig. 12. DM code reading quality. (a) X/Y direction printing growth; (b) contrast

Fig. 13. Surface scratches and friction coefficient curves of DM codes. (a) Surface scratches; (b) friction coefficient curves

Fig. 14. Comparison of scratches on the surface of laser marking DM codes in atmospheric environment and nitrogen-filled environment. (a) Atmospheric environment; (b) nitrogen-filled environment
|
Table 1. Preparation parameters of nitriding samples
|
Table 2. Mass fraction of elements of each sample line scan
|
Table 3. Average Vickers hardness and dimensional wear coefficient on the sample surface
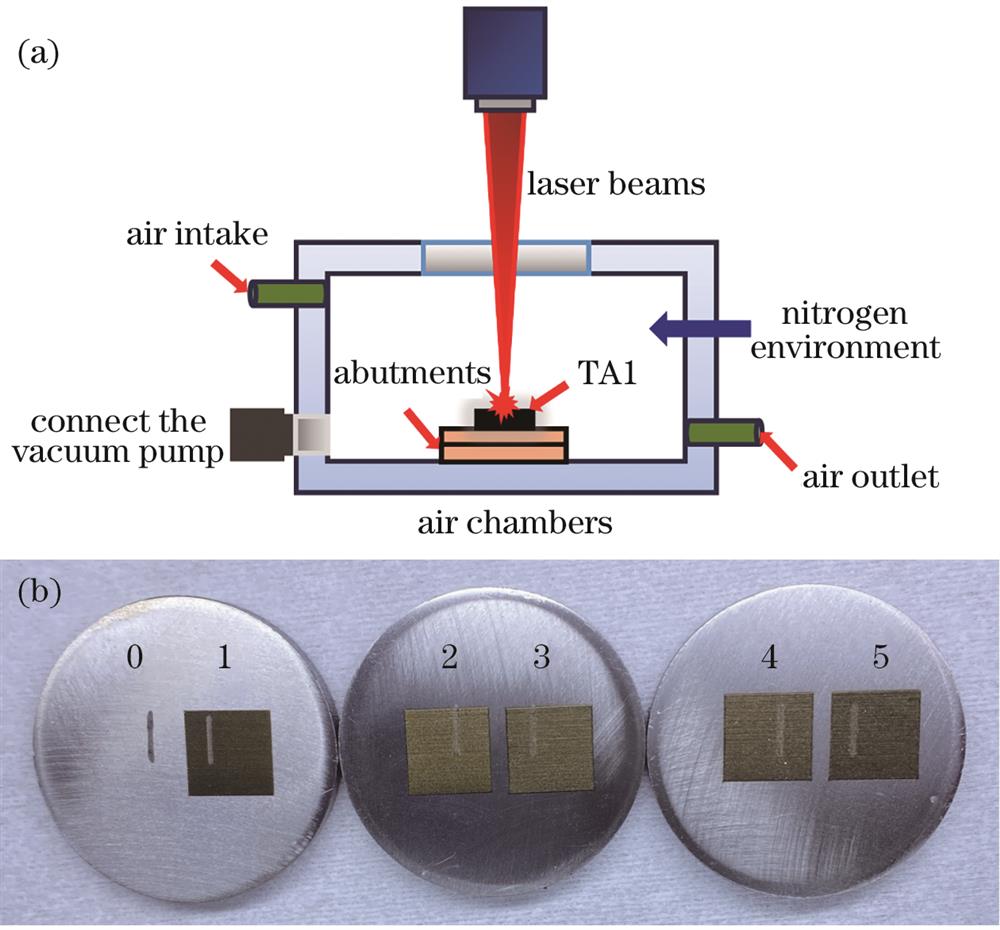
Set citation alerts for the article
Please enter your email address