Xingbang Zhao, Zhengminqing Li, Xiaofeng Yu, Yong Liu, Letian Li. Point Cloud Registration and Modeling Method for Gear Surfaces Based on Laser and Vision Fusion[J]. Laser & Optoelectronics Progress, 2025, 62(8): 0815013

Search by keywords or author
- Laser & Optoelectronics Progress
- Vol. 62, Issue 8, 0815013 (2025)
Note: This section is automatically generated by AI . The website and platform operators shall not be liable for any commercial or legal consequences arising from your use of AI generated content on this website. Please be aware of this.
Abstract
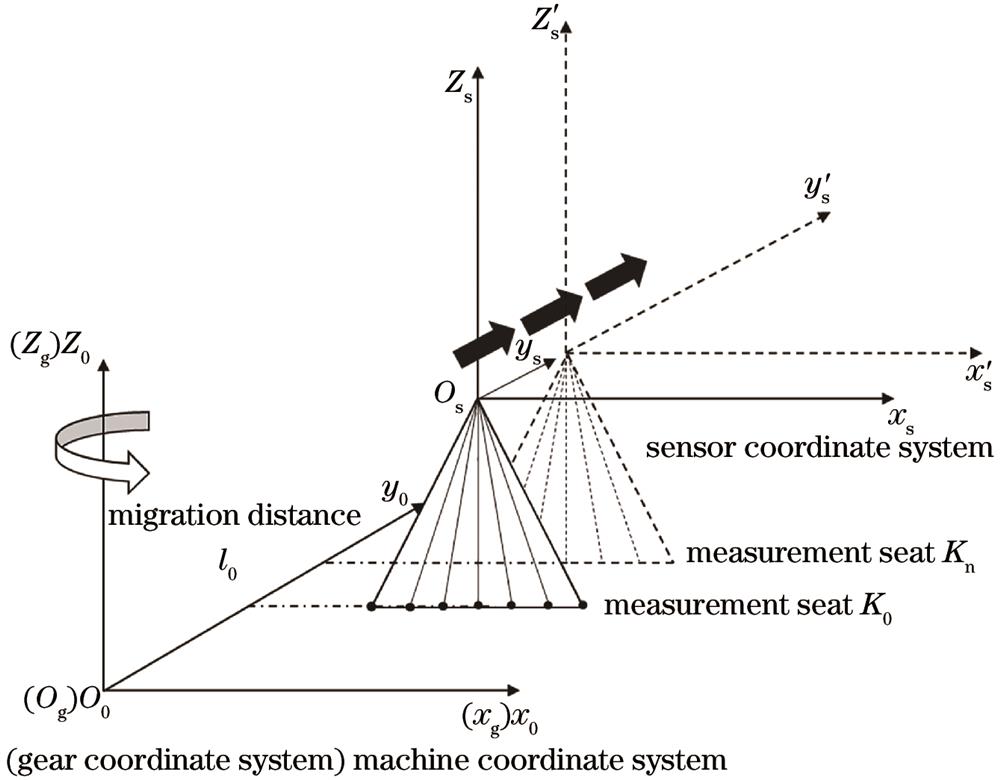
Set citation alerts for the article
Please enter your email address