Lu Pan, Chenglin Zhang, Liang Wang, Qihui Liu, Gang Wang. Crack Formation Law and Mechanism in Selective Laser Melting of 316L Stainless Steels[J]. Laser & Optoelectronics Progress, 2019, 56(10): 101401

Search by keywords or author
- Laser & Optoelectronics Progress
- Vol. 56, Issue 10, 101401 (2019)

Fig. 1. Morphology of 316L stainless steel powder
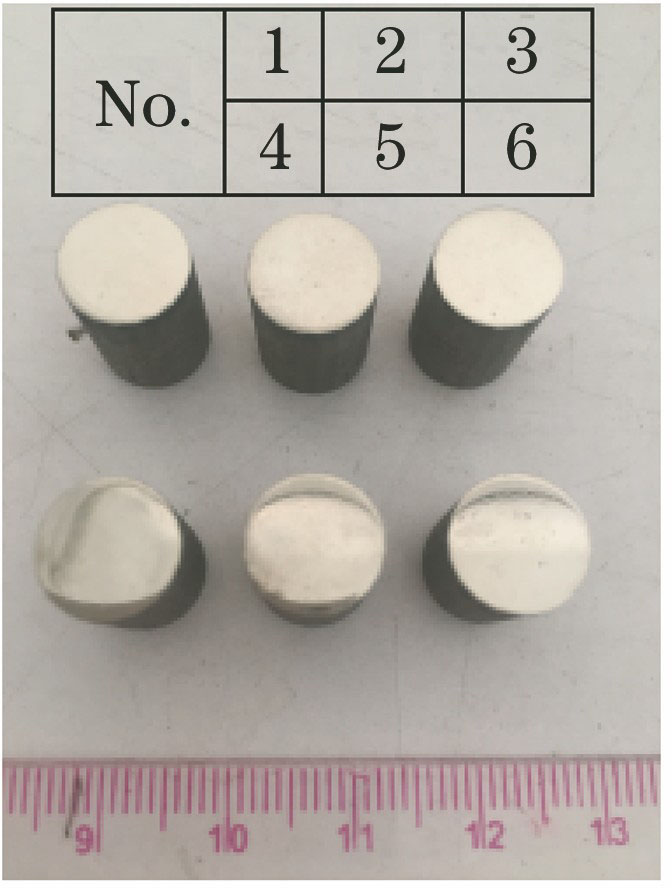
Fig. 2. Macrographs of printed samples

Fig. 3. Cracks under different process parameters. (a)Line energy density of 181.8 J/m; (b) line energy density of 250 J/m; (c) line energy density of 475 J/m; (d) line energy density of 583.3 J/m; (e) line energy density of 633.3 J/m; (f) line energy density of 875 J/m

Fig. 4. Defects and defect proportion versus line energy density. (a) Different defects versus line energy density; (b) different crack defects versus line energy density

Fig. 5. Overall crack morphology

Fig. 6. Local amplification of cracks. (a) Area C; (b)area D

Fig. 7. Typical crack positions

Fig. 8. EBSD diagram of crack. (a) Morphologies and sizes of grains at cracks; (b) precipitated phase compositions at cracks

Fig. 9. Micromorphology at end of hot crack in 316L steel

Fig. 10. Defect maps. (a) Digital photographic physical map; (b) surface morphology of the sample
|
Table 1. Chemical composition of 316L stainless steel used in SLM forming (mass fraction, %)
|
Table 2. Process parameters for SLM formation
|
Table 3. EDS analysis results of typical pointsinside and outside cracks (mass fraction, %)
|
Table 4. EDS analysis results of typical points inside and outside cracks

Set citation alerts for the article
Please enter your email address