Chupeng Zhang, Linxiao Yang, Han Xu, Jiazheng Sun, Yingxue Li, Xiao Chen. Development and Application of Chemical Mechanical Polishing Surface-Pressure Distribution Detection Device Based on Thin-Film Sensors[J]. Laser & Optoelectronics Progress, 2023, 60(15): 1512002

Search by keywords or author
- Laser & Optoelectronics Progress
- Vol. 60, Issue 15, 1512002 (2023)
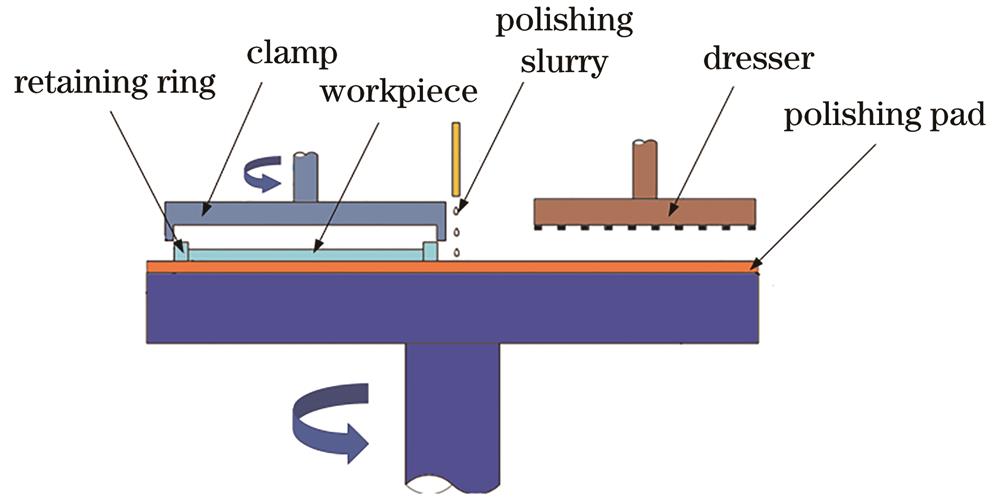
Fig. 1. CMP system schematic diagram
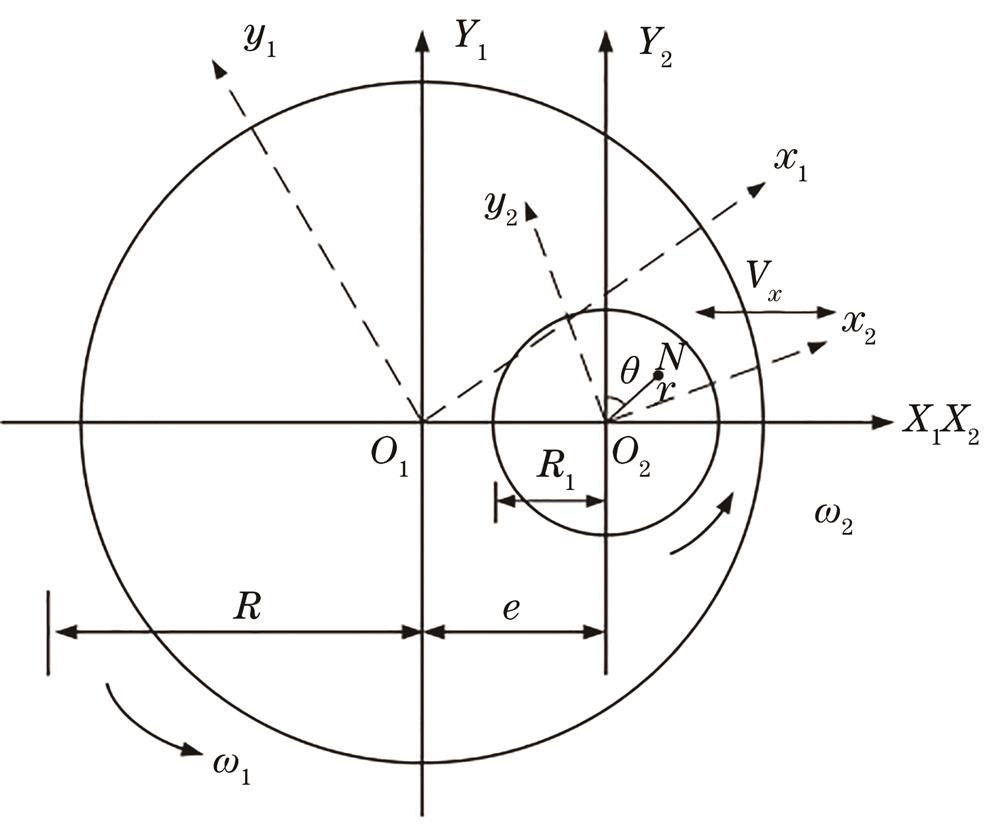
Fig. 2. Motion relation diagram

Fig. 3. Contact pressure model of point N

Fig. 4. Contact diagram of workpiece and plate

Fig. 5. Resistive strain gauge layout

Fig. 6. Thin-film piezoresistive sensor patch layout

Fig. 7. Acquisition system hardware diagram

Fig. 8. Schematic diagram of pressure distribution in-situ detection device

Fig. 9. Cloud map without pressure

Fig. 10. Cloud map with single weight

Fig. 11. Calibration experiment diagram

Fig. 12. Pressure-load curve

Fig. 13. Simulation results. (a) Stress distribution; (b) stress distribution along the radial direction

Fig. 14. Change of pressure distribution with increasing load

Fig. 15. Change of contact status with increasing load (a) Contact pressure distribution under small load; (b) contact pressure distribution under large load

Fig. 16. Grinding experiment platform

Fig. 17. Experimental data acquisition path

Fig. 18. Change in pressure distribution under different loads during grinding

Fig. 19. Change of polishing pad surface shape with increasing grinding time

Fig. 20. Change of mean and standard deviation of pressure with increasing grinding time

Fig. 21. Change of pressure distribution on path 1 and path 2 with grinding time. (a) 5 kg; (b) 6 kg; (c) 7 kg
|
Table 1. Simulation model material parameters and geometric dimensions
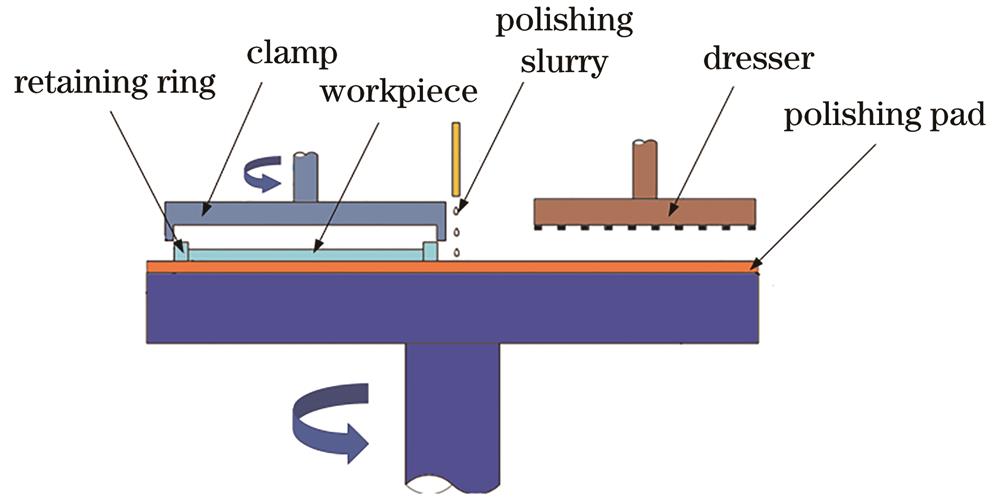
Set citation alerts for the article
Please enter your email address