Xiaohong QI, Xiaokang LIANG, Zheng XIAO, Zhengyu WEI, Xinwei LIU, Zhuangzhuang LIU. Mechanical behavior of lattice-reinforced porous structures of Inconel 718 fabricated by laser additive manufacturing (invited)[J]. Infrared and Laser Engineering, 2024, 53(11): 20240432

Search by keywords or author
- Infrared and Laser Engineering
- Vol. 53, Issue 11, 20240432 (2024)
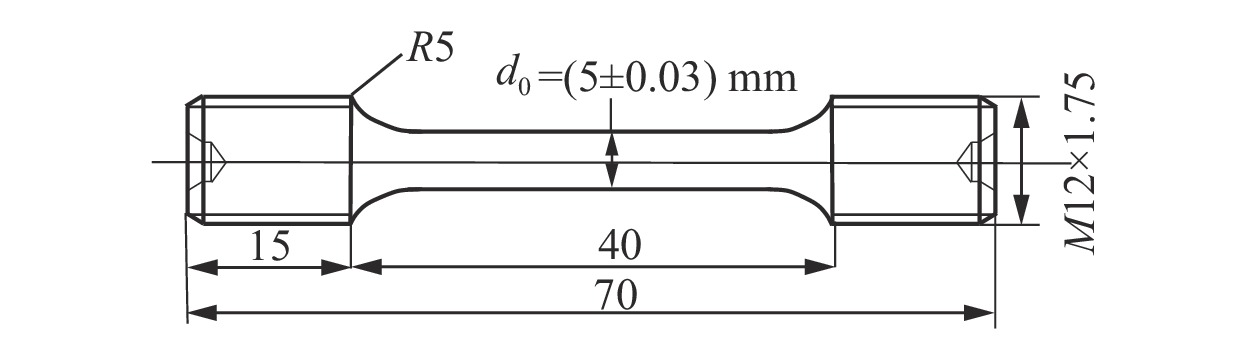
Fig. 1. Drawing of tensile specimen dimensions

Fig. 2. The relationship between porosity and planar energy density

Fig. 3. Porosity distribution of the samples under different planar energy densities(CT scan results). (a) 0.38 J/mm2-55.65%; (b) 0.83 J/mm2-31.97%; (c) 0.92 J/mm2-21.97%; (d) 1.22 J/mm2-10.33%

Fig. 4. Tensile-tested samples in the as-built condition. (a) Planar energy density of 0.38 J/mm2; (b) Planar energy density of 1.22 J/mm2

Fig. 5. Mechanical properties in the as-built condition. (a) Variation of tensile strength and elongation at break with planar energy density; (b) The relationship between tensile strength and porosity
![Schematic diagram of lattice-reinforced porous structure: (a) Schematic diagram of gyroid-sheet surface[19]; (b) 3D Model of lattice-reinforced porous structure from CT scan](/Images/icon/loading.gif)
Fig. 6. Schematic diagram of lattice-reinforced porous structure: (a) Schematic diagram of gyroid-sheet surface[19]; (b) 3D Model of lattice-reinforced porous structure from CT scan

Fig. 7. CT scan images of lattice-reinforced samples. (a) G5; (b) G7; (c) G9

Fig. 8. Mechanical properties of G5-G9 lattice-reinforced samples. (a) Tensile curves of G5-G9 lattice-reinforced porous structure samples and porous structure samples; (b) Tensile strength and elongation at break of G5-G9 lattice-reinforced porous structure samples

Fig. 9. 270x SEM images of fracture of porous structures and lattice-reinforced porous structure samples. (a) Morphology of the fracture of the porous structure sample; (b) Morphology of the fracture of the G5 sample; (c) Morphology of the fracture of the G7 sample; (d) Morphology of the fracture of the G9 sample

Fig. 10. Stress distribution contour maps for models with different porosity

Fig. 11. Schematic diagrams of models with different pore sizes

Fig. 12. Stress distribution contour maps of models with different pore sizes

Fig. 13. Schematic diagram of lattice-reinforced structure

Fig. 14. Stress distribution contour map of the lattice-reinforced model

Fig. 15. Lattice-reinforced porous structure models

Fig. 16. Stress distribution contour map of the lattice-reinforced structure
|
Table 1. Composition of IN718 alloy(wt.%)
|
Table 2. Orthogonal experiment table
|
|
Table 4. Simulation model parameters for different porosities
|
Table 5. Different pore sizes and compositions
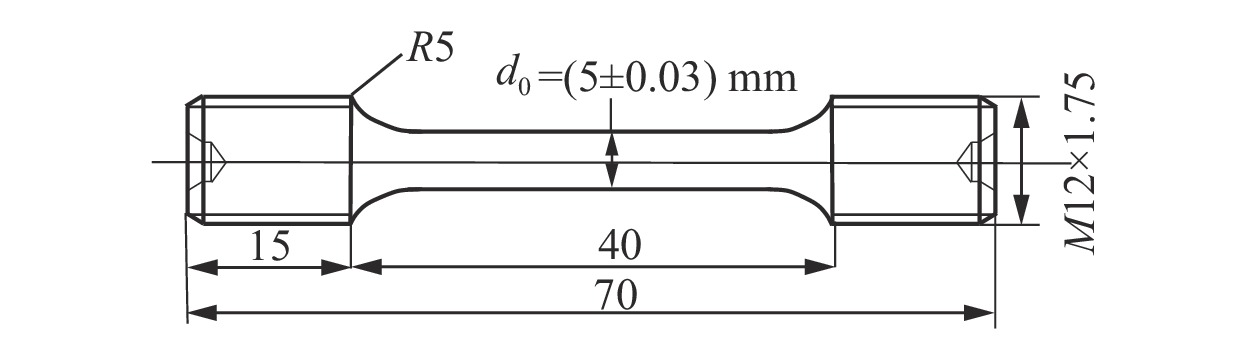
Set citation alerts for the article
Please enter your email address