Zhonghan Yu, Li Yin, Yanlong Xu, Yuantao Zhao, Tao Jiang, Jianmin Ling, Wenge Li. Research Progress of Laser Derusting Technology in Coating Pretreatment[J]. Laser & Optoelectronics Progress, 2024, 61(5): 0500006

Search by keywords or author
- Laser & Optoelectronics Progress
- Vol. 61, Issue 5, 0500006 (2024)
![Three adhesion forces between surface particles and substrate. (a) Van der Waals force; (b) capillary condensing force; (c) electrostatic double layer force [11]](/richHtml/lop/2024/61/5/0500006/img_01.jpg)
Fig. 1. Three adhesion forces between surface particles and substrate. (a) Van der Waals force; (b) capillary condensing force; (c) electrostatic double layer force [11]
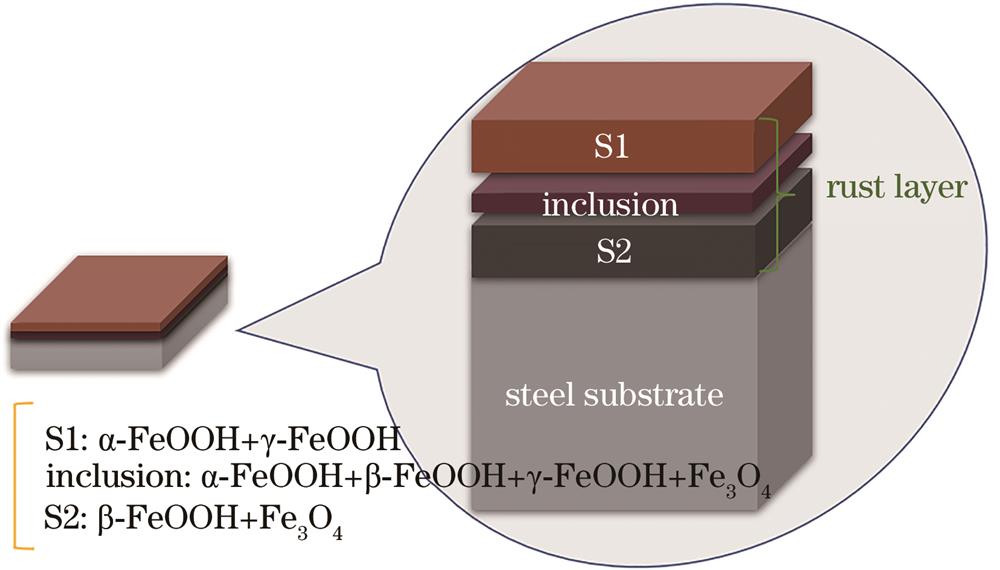
Fig. 2. Structure diagram of corroded layer on steel surface
![Bright spot characteristics. (a) Bright spot morphology[32]; (b) pulse laser spot energy distribution[4]](/Images/icon/loading.gif)
Fig. 3. Bright spot characteristics. (a) Bright spot morphology[32]; (b) pulse laser spot energy distribution[4]

Fig. 4. Lapping effect diagram. (a) Schematic diagram of surface covering; (b) schematic diagram of spot lap rate
![Actual rendering of laser derusting under different defocus quantities[45]. (a) +3 mm; (b) +2 mm; (c) 0 mm; (d)-2 mm; (e)-3 mm](/Images/icon/loading.gif)
Fig. 5. Actual rendering of laser derusting under different defocus quantities[45]. (a) +3 mm; (b) +2 mm; (c) 0 mm; (d)-2 mm; (e)-3 mm
![Diagram of laser intelligent rust removal equipment[46]](/Images/icon/loading.gif)
Fig. 6. Diagram of laser intelligent rust removal equipment[46]
![Working flow chart[46]](/Images/icon/loading.gif)
Fig. 7. Working flow chart[46]
![Schematic diagram of laser cleaning monitoring structure[55]](/Images/icon/loading.gif)
Fig. 8. Schematic diagram of laser cleaning monitoring structure[55]
|
Table 1. Advantages and disadvantages of derusting technology
|
Table 2. Research history of laser derusting theory
|
Table 3. Typical laser cleaning techniques
|
Table 4. Laser derusting equipment combined with related technologies
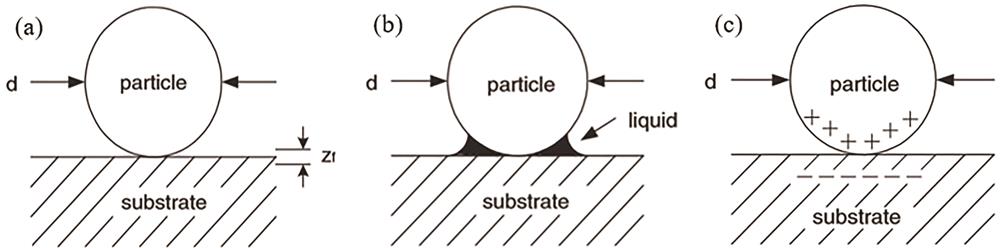
Set citation alerts for the article
Please enter your email address