
- Journal of Inorganic Materials
- Vol. 36, Issue 10, 1118 (2021)
Abstract
Keywords
Scintillation materials are widely used in high energy physics, nuclear medicine imaging, security techniques and other X/γ ray or particle beam detection devices[
There are many factors affecting scintillation property of materials. Structural design and scintillation property of materials are sometimes shaped by co-doping. When Ce3+ substitutes Sr2+ in the Ce:SrHfO3 ceramics, the charge imbalance causes the production of Ce4+ and interstitial oxygen, which leads to deterioration of scintillation property. By aluminum co-doping, Al3+ substitutes for Hf4+ and the effective charge compensation increases the Ce3+/Ce4+ ratio[
In this work, Ce,Y:SrHfO3 powders were prepared by solid-state synthesis. Ce,Y:SrHfO3 ceramics were successfully fabricated by vacuum pre-sintering combined with hot isostatic pressing (HIP). The influence of calcination temperature on the phase composition, particle size and morphology of the powders was systematically investigated. In addition, the crystal structure, luminescence, and scintillation property of Ce,Y:SrHfO3 ceramics were also investigated.
1 Experimental
The Ce0.005,Y0.005:Sr0.995Hf0.995O3 powders were prepared by solid-state reaction. Commercial powders of HfO2 (99.99%), SrCO3 (99.95%), CeO2 (99.99%), and Y2O3 (99.99%) were used as starting materials. These powders were weighed according to the formula of Ce0.005,Y0.005:Sr0.995Hf0.995O3 following a mixing and ball-milling process for 12 h in ethanol solvent at a rotation speed of 130 r/min. The obtained slurries were dried and sieved. Then the mixed powders were calcined in alumina crucibles at different temperatures for 8 h to obtain Ce0.005,Y0.005:Sr0.995Hf0.995O3 powders. Mixed powders were pressed into discs and cold isostatically pressed under 250 MPa. A part of the Ce0.005,Y0.005: Sr0.995Hf0.995O3 discs were further vacuum-sintered at 1850 ℃ for 20 h. The other part of discs were pre- sintered at 1450-1650 ℃ for 2 h in a vacuum furnace (10-5 Pa) and subsequently hot isostatically pressed at 1800 ℃ in Ar and under the pressure of 200 MPa for 3 h. Finally, all Ce0.005,Y0.005:Sr0.995Hf0.995O3 ceramics were double mirror-polished to the thickness of 1 mm for following characterization. In order to get sharp microstructure pictures of grain boundaries, a thermal etching process was applied before SEM, in which the ceramic sample was kept at 1400 ℃ for 3 h in air.
The structural phase of the calcined powders was identified by the X-ray diffraction (XRD, Cu-Kα radiation 0.154 nm Mode-l D/max2200PC, Rigaku, Japan). The microstructure and morphology of powders were observed by field emission scanning electron microscope (FESEM, S-4800, Hitachi, Japan). Morphology of the ceramics was observed by field emission scanning electron microscope (FESEM, SU8220, Hitachi, Japan). The specific surface area analysis was conducted by Norcross ASAP 2010 micromeritics, using N2 as an absorbate gas at 77 K. The density of ceramics was measured by the Archimedes method using deionized water as the immersion medium. The X-ray excited luminescence (XEL) measurements were conducted by a home-made X-ray excited luminescence spectrometer. The excitation F30III-2 X-ray tube was operated at 70 kV with a tungsten target. Light yield measurement was accomplished by the measurement of pulse height spectra under the 662 keV γ-ray excitation (137Cs source) and detection by a Hamamatsu R878 photomultiplier with 1 μs shaping time.
2 Results and discussion
Fig. 1(a-f) shows the FESEM micrographs of four types of raw material powders, the ball-milled powder mixture and the powder calcined at 1200 ℃ for 8 h. It can be seen from Fig. 1(a, b) that the HfO2 and SrCO3 powders consist of nearly spherical particles with the uniform shape and particle size. The CeO2 and Y2O3 powders have the block structure with the particle size larger than 1 μm as shown in Fig. 1(c, d). After the ball milling, the powders with large particle size are effectively broken into small particles, and different powders are well dispersed and uniformly mixed as shown in Fig. 1(e). After being calcined at 1200 ℃ for 8 h in air, Ce,Y:SrHfO3 powder is slightly agglomerated and of fairly uniform size, with an average particle size of approximate 152 nm as shown in Fig. 1(f), which possesses a strong sintering activity. Compared with the standard XRD pattern of orthorhombic SrHfO3 (PDF#45- 0212), the Ce,Y:SrHfO3 powders consist of the SrHfO3 phase without other intermediate phases detected, as shown in Fig. 1(g). The diffraction peaks of the calcined powders slightly move to the high angle, which is caused by the fact that smaller trivalent cerium ions enter the lattice to replace the position of the bivalent strontium ions. First,to fabricate fully dense ceramic, a long-time vacuum sintering was implemented. As shown in Fig. 1(h), the Ce,Y:SrHfO3 ceramics sintered at 1800 ℃ for 20 h in vacuum appear opaque. The average grain size of Ce,Y:SrHfO3 ceramics was measured to be about 28.6 μm. The large grains arranged in disorder cause severe birefringent effect in asymmetric system and reduce the optical transmittance of the ceramics. Except for the large grain size, a large number of intracrystalline and intergranular pores are observed in Ce,Y:SrHfO3 ceramics. It is well known that the pores in the microstructures of transparent ceramics are the primary light scattering sources. In order to further improve the optical quality of ceramics, an alternative way of preparation consisting in the low-temperature vacuum pre-sintering and HIP post-treatment was used, which was expected to eliminate residual pores while maintaining fine grains.
Figure .FESEM micrographs of the starting powders ((a) HfO2, (b) SrCO3, (c) CeO2, (d) Y2O3, (e) ball-milled powder mixture, (f) Ce,Y:SrHfO3 powder calcined at 1200 ℃ for 8 h), (g) XRD patterns of the calcined powder, and (h) FESEM micrograph of the Ce,Y:SrHfO3 ceramics fabricated by vacuum sintering
Fig. 2(a-e) shows the FESEM microstructures of the thermally etched surfaces of the Ce,Y:SrHfO3 ceramics pre-sintered at different temperatures for 2 h. It can be seen that the grain boundaries of Ce,Y:SrHfO3 ceramics pre-sintered at different temperatures are clearly visible, and neither impurities nor the second phase appears at the grain boundaries. With the increase of pre-sintering temperature, the small pores between grains gathered into bigger ones and were then gradually eliminated. The grain size becomes larger, and the ceramics become more compact. When the pre-sintering temperature reaches 1650 ℃, the ceramics are basically compact but some intracrystalline pores appear at this temperature. The relative densities of the Ce,Y:SrHfO3 ceramics before and after HIP post-treatment at different pre-sintering temperatures and the average grain size of the pre-sintered body calculated from the FESEM microstructures are shown in Fig. 2(f). With the sintering temperature increasing from 1450 to 1650 ℃, the relative density of the pre-sintered ceramic increases from 89.8% to 98.0%, and the average grain size of ceramics increases from 0.4 to 1.4 mm. Especially when the pre-sintering temperature exceeds 1550 ℃, the grains grow rapidly. The relative density of HIP post-treated Ce,Y:SrHfO3 ceramics first increases and then decreases, because the higher pre- sintering temperature leads to the larger grain size, which means lower driving force of grain boundary migration in HIP post-treatment. Meanwhile high pre-sintering temperature produces intracrystalline pores, which can hardly be eliminated in HIP treatment.
Figure .FESEM images of the thermally etched surfaces of the Ce/Y:SrHfO3 ceramics pre-sintered at different temperatures for 2 h (a) 1450 ℃; (b) 1500 ℃; (c) 1550 ℃; (d) 1600 ℃; (e) 1650 ℃; (f) Relative densities and average grain sizes of the Ce,Y:SrHfO3 ceramics with different pre-sintering temperatures
Fig. 3(a) shows the photograph of the Ce,Y:SrHfO3 ceramics vacuum-sintered at different temperatures for 2 h combined with the HIP post-treatment at 1800 ℃ for 3 h. The Ce,Y:SrHfO3 ceramics pre-sintered at 1450 ℃ is still opaque after HIP post-treatment due to the insufficient densification and connected pores, which cannot be compressed with the aid of pressure. The Ce,Y:SrHfO3 ceramics pre-sintered at 1600 and 1650 ℃ are also opaque after HIP post-treatment possibly due to the low driving force caused by large grain size and the remainning intracrystalline pores in the ceramics. After the HIP post-treatment, Ce,Y:SrHfO3 pre-sintered at temperatures within 1500 and 1550 ℃ become transparent and the text below the ceramics is legible. It indicates that the pre-sintering temperature has an important influence on the transparency of the ceramic. The in-line transmittance curves of the HIP post-treated Ce,Y:SrHfO3 ceramics pre-sintered at 1500 and 1550 ℃ are shown in Fig. 3(b), and the former has the highest transmittance of 22% at 800 nm. Scintillation materials used in most fields like high energy physics and nuclear medicine equipment must be transparent, otherwise the visible light transformed from high energy rays is supposed to be self-absorbed and cannot reach the detectors behind.
Figure .(a) Photograph of the Ce,Y:SrHfO3 ceramics vacuum- sintered at different temperatures combined with the HIP post- treatment and (b) in-line transmittance of the HIP post-treated Ce,Y:SrHfO3 ceramics (1 mm thickness) pre-sintered at 1500 and 1550 ℃, respectively
The microstructure of the ceramic with the best transmittance was also analyzed as shown in Fig. 4. The FESEM micrographs of thermally etched surfaces and fractured surfaces of the HIP post-treated Ce,Y:SrHfO3 ceramics pre-sintered at 1500 ℃ show very tiny number of pores. Compared with pre-sintered Ce,Y:SrHfO3 ceramics, the Ce,Y:SrHfO3 ceramics after HIP treatment show higher density and larger average grain size of 3.4 μm, which is still far smaller than that of the ceramics prepared via long-time vacuum sintering. The effective elimination of pores and the retention of fine grains are the key points for the preparation of transparent Ce,Y:SrHfO3 ceramics by HIP treatment.
Figure .FESEM micrographs of (a) thermally etched surfaces and (b) fractured surfaces of HIP post-treated Ce,Y:SrHfO3 ceramics pre-sintered at 1500 ℃
The luminescence and scintillation property of the sample with the best transmittance were evaluated. Fig. 5(a) shows the XEL spectra (X-ray Excited Luminescence, XEL) of the HIP post-treated Ce,Y:SrHfO3 ceramics pre-sintered at 1500 ℃ and BGO single crystal at room temperature. The emission peak of Ce,Y:SrHfO3 is situated at around 400 nm originating from the 5d-4f emission of Ce3+. Comparing the integral of the emission spectra, the light output of Ce,Y:SrHfO3 ceramics is 3.3 times higher than that of BGO commercial crystal. Fig. 5(b) shows the pulse height spectrum of the HIP post-treated Ce,Y:SrHfO3 ceramics pre-sintered at 1500 ℃ under the 662 keV γ-ray excitation of 137Cs source with 1 μs shaping time. Ce,Y:SrHfO3 ceramics have a light yield of approximately 3700 ph/MeV which is less than half of that of BGO crystals. Comparison of overall scintillation efficiency derived from XEL spectra integrals and light yield measured in Ce,Y:SrHfO3 ceramics and BGO crystal points to existing very slow components in the scintillation response of the former. The oxygen vacancies and related electron traps caused by reductive preparation atmosphere may be one of the reasons, and further study is needed for material optimization.
Figure .(a) XEL spectra and (b) pulse height spectrum of the HIP post-treated Ce,Y:SrHfO3 ceramics pre-sintered at 1550 ℃
3 Conclusion
In this work, Ce,Y:SrHfO3 powders were prepared by solid-state synthesis using the commercial HfO2, SrCO3, CeO2, and Y2O3 as the starting materials. Pure SrHfO3 phase is formed at 1200 ℃ for 8 h duration in air. Ce,Y:SrHfO3 ceramics are successfully fabricated by (i) traditional long-time vacuum sintering and (ii) short-time vacuum pre- sintering combined with HIP post-treatment. The Ce,Y:SrHfO3 ceramics sintered in vacuum at 1800 ℃ for 20 h are opaque due to the large grain size and residual pores. For the second preparation method, the average grain size of the pre-sintered Ce,Y:SrHfO3 ceramics increases from 0.4 to 1.4 μm with the increase of pre-sintering temperature from 1450 to 1650 ℃. Subsequent HIP post-treatment successfully eliminates the pores, and the fine grain size is retained, both of which improve the optical quality of ceramics. The Ce,Y:SrHfO3 ceramics pre-sintered at 1500 ℃ for 2 h with HIP post-treatment at 1800 ℃ for 3 h show the highest in-line transmittance of 22% at 800 nm. Overall scintillation efficiency derived from XEL spectra integral is 3.3 times higher than that of BGO crystals, while its light yield value is 3700 ph/MeV. The latter points to the presence of intense slow components in the scintillation response and requires further study.
References
[8] T YANAGIDA, A FUKABORI, A FUJIMOTO Y et al. Scintillation properties of transparent Lu3Al5O12(LuAG) ceramics doped with different concentrations of Pr3+. Physica Status Solidi A-Applications and Materials Science, 8, 140-143(2011).
[18] P JOANNA J, E ZYCH. Microwave-assisted hydrothermal synthesis and spectroscopic characteristics of Lu4Hf3O12:Pr scintillator. RSC Advances, 6, 5610-561(2016).
[24] E MIHÓKOVÁ, V JARÝ, M FASOLI et al. Delayed recombination and excited state ionization of the Ce3+ activator in the SrHfO3 host. Chemical Physics Letters, 7, 228-231(2013).
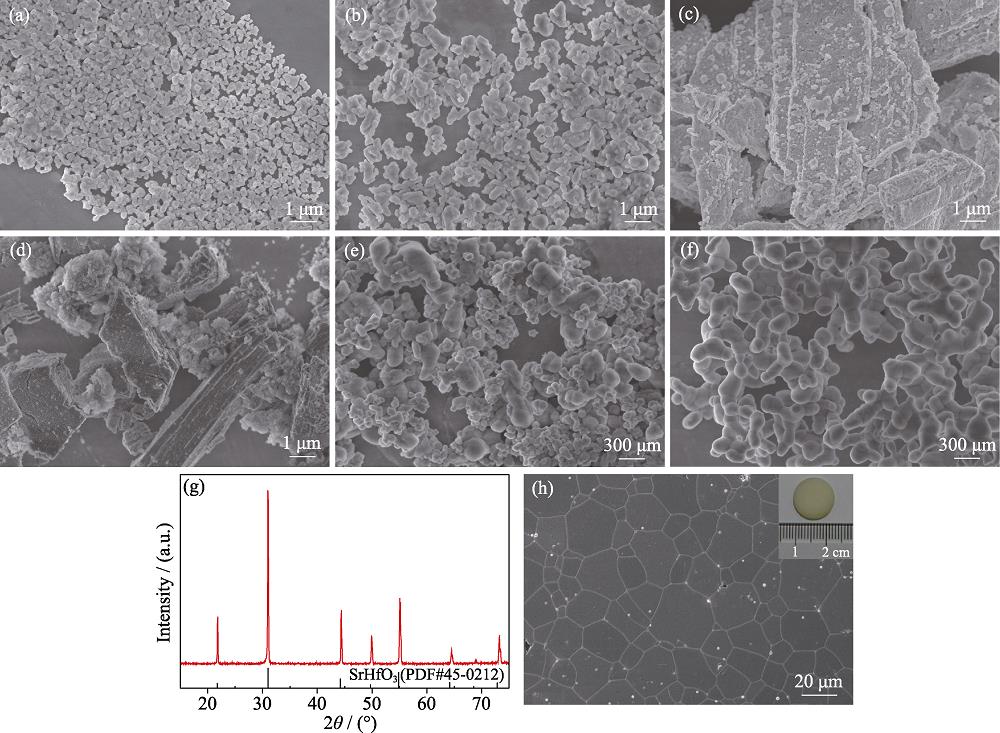
Set citation alerts for the article
Please enter your email address