Hao Xiao, Jian Huang, Peng Wang, Peixin Xu, Yifei Xu, Dongyue Zhang, Borui Du. Microstructure Evolution and Corrosion Resistance of FeCoCrNiMo High‐Entropy Alloy Coatings Fabricated via Extremely High‐Speed Laser Cladding[J]. Chinese Journal of Lasers, 2025, 52(4): 0402203

Search by keywords or author
- Chinese Journal of Lasers
- Vol. 52, Issue 4, 0402203 (2025)
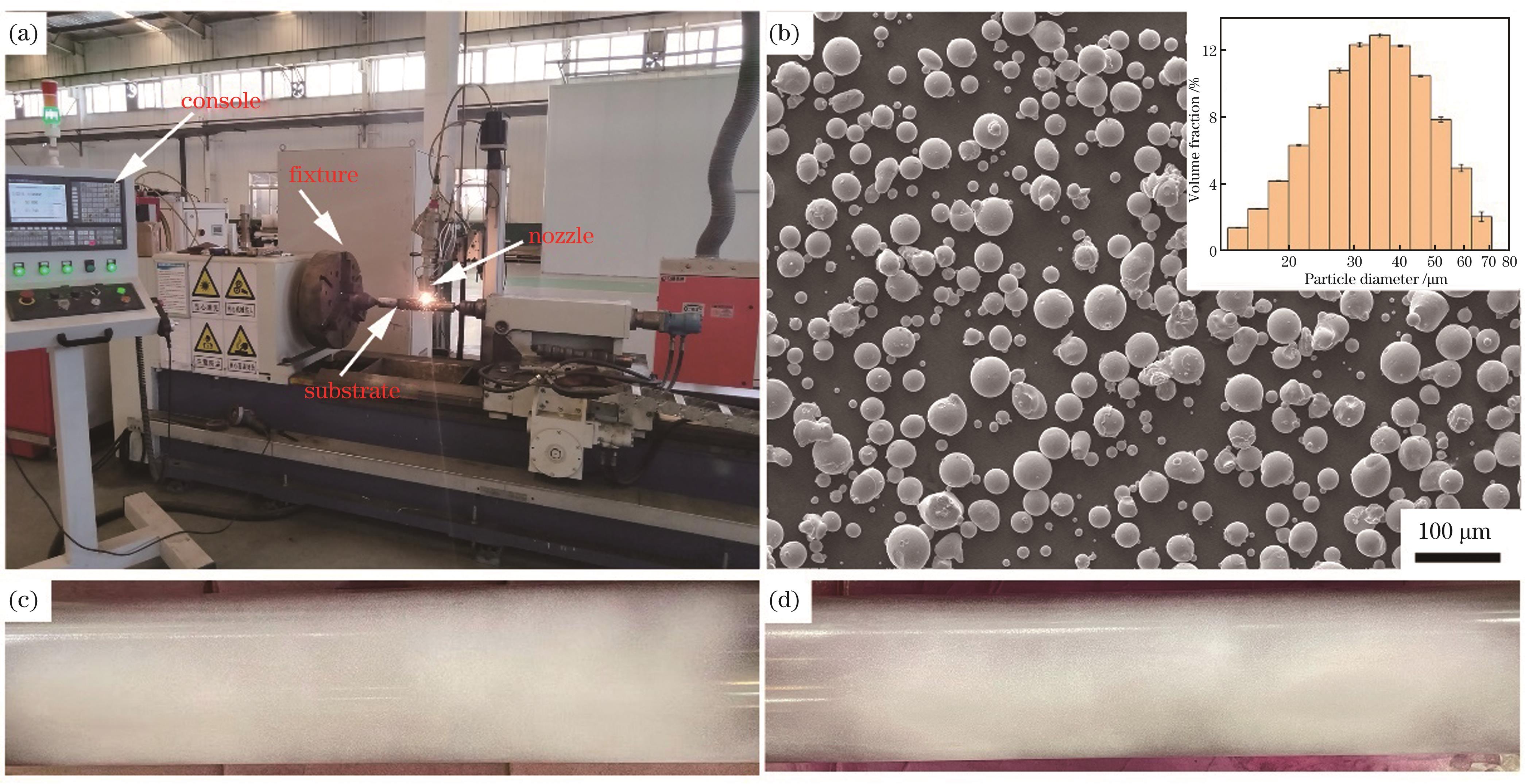
Fig. 1. Extremely high-speed laser cladding equipment and powder raw material. (a) Extremely high-speed laser cladding equipment; (b) FeCoCrNiMo high-entropy alloy powder morphology and particle diameter distribution; (c) surface defect result of polished 316L primer; (d) surface defect result of polished 304 coating
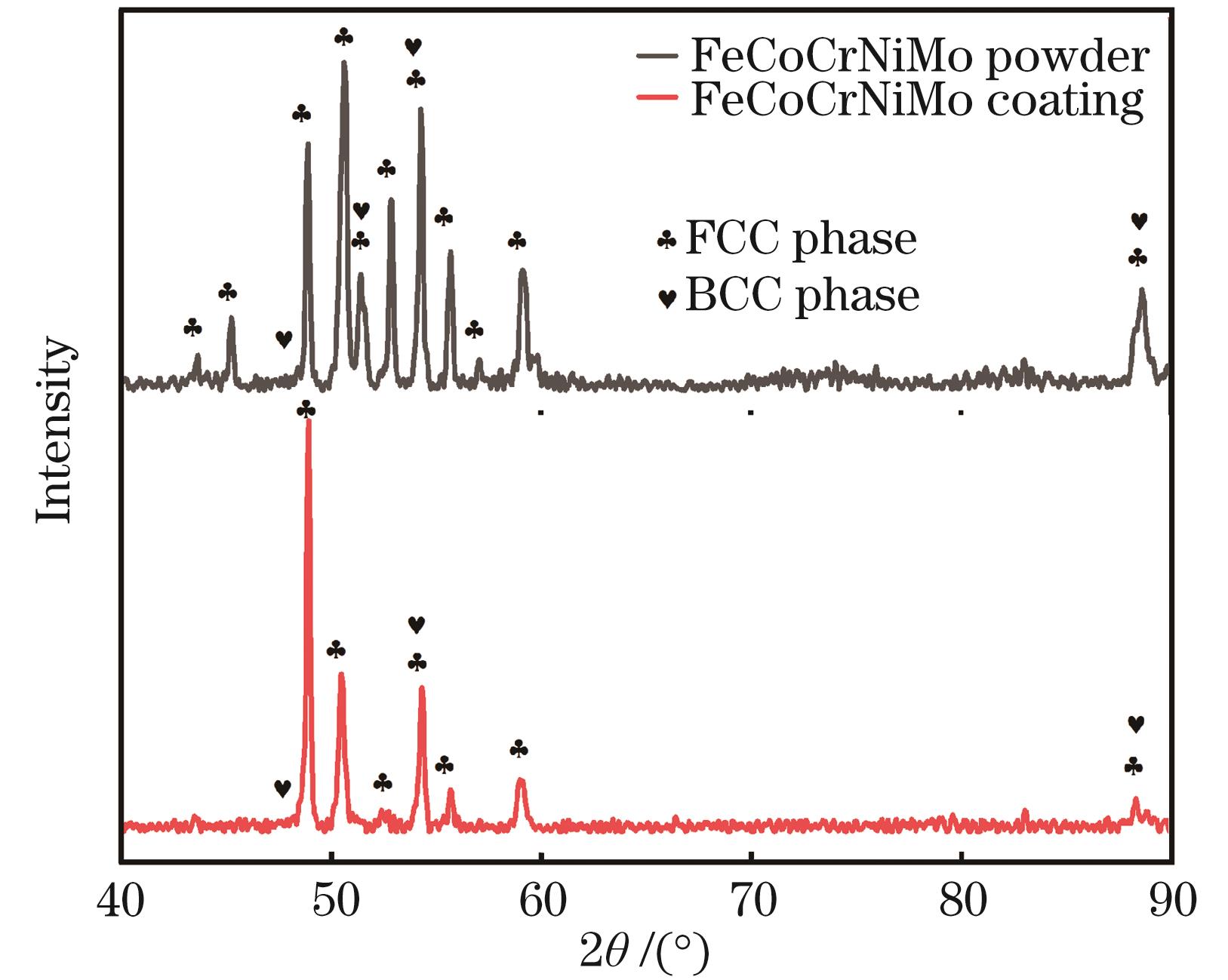
Fig. 2. XRD spectra of FeCoCrNiMo powder and coating

Fig. 3. Microstructes of FeCoCrNiMo high-entropy alloy coating captured by scanning transmission electron microscopy. (a) STEM images of the bright field of the coatings and the corresponding STEM-EDS maps; (b) selected-area diffraction pattern of superlattice points of the BCC precipitated phase; (c) selected-area diffraction pattern of superlattice points of the FCC matrix phase

Fig. 4. SEM microstructure distribution of FeCoCrNiMo high-entropy alloy coatings. (a) Whole coating; (b) the top region of the coating; (c) the middle region of the coating; (d) the overlap position

Fig. 5. Detection results and optical microscopy morphology of FeCoCrNiMo high-entropy alloy coating. (a)(b) Detection results of the cracked coatings without using 316L stainless steel as a primer, where the figure (a) corresponds to the cladding parameters of P=1.5 kW and u=15 m/min and the figure (b) corresponds to the cladding parameters of P=1.5 kW and u=5 m/min; (c) detection result of the uncracked coating using 316L stainless steel as a primer, corresponding to the cladding parameters of P=1.5 kW and u=5 m/min; (d)(e) optical microscopy morphology of the cracked coatings without using 316L stainless steel as a primer, where the figure (d) corresponds to the cladding parameters of P=1.5 kW and u=15 m/min and the figure (b) corresponds to the cladding parameters of P=1.5 kW and u=5 m/min; (f) optical microscopy morphology of the uncracked coating using 316L stainless steel as a primer, corresponding to the cladding parameters of P=1.5 kW and u=5 m/min

Fig. 6. Cross-sectional microstructure distributions of FeCoCrNiMo high-entropy alloy cracked coatings produced under different laser cladding linear velocities (No 316L stainless steel was used as a primer). (a) (c) Cross-sectional and local morphology of reticulated cracks in high-entropy alloy coating produced at a linear velocity of 15 m/min; (b) (d) cross-sectional and local morphology of stripe cracks in high-entropy alloy coating produced at a linear velocity of 5 m/min

Fig. 7. Microstructure distributions of FeCoCrNiMo high-entropy alloy coating fabricated by EHLC on 316L primer layer (P=1.5 kW, u=5 m/min). (a) Whole coating; (b) the top region of the coating; (c) the middle region of the coating

Fig. 8. Vickers hardness distribution of FeCoCrNiMo high-entropy alloy coatings produced by different linear velocities

Fig. 9. FCC phase percentage and microstructure distribution in local regions of FeCoCrNiMo high-entropy alloy coatings fabricated at different linear velocities. (a) FCC phase percentage; (b)(d) local microstructure distribution and local surface scanning results of the coating fabricated at linear velocityof 15 m/min; (c)(e) local microstructure distribution and local surface scanning results of the coating fabricated at linear velocity of 5 m/min

Fig. 10. Potentiodynamic polarisation curves and AC impedance diagram of FeCoCrNiMo high-entropy alloy and 304 stainless steel coatings. (a) Potentiodynamic polarisation curves; (b) AC impedance diagram

Fig. 11. Local corrosion morphology of FeCoCrNiMo high-entropy alloy coatings following neutral salt spray experiments of different durations
|
Table 1. Chemical composition of FeCoCrNiMo high-entropy alloy powder
|
Table 2. Cladding process parameters of 316L stainless steel primer and 304 stainless steel coating
|
Table 3. Extremely high-speed laser cladding (EHLC) process parameters for FeCoCrNiMo cracked coatings without using 316L stainless steel as a primer
|
Table 4. EHLC process parameters for FeCoCrNiMo uncracked coating using 316L stainless steel as a primer
|
Table 5. Fitting parameters for polarisation curves
|
Table 6. Electrochemical impedance spectrum fitting results
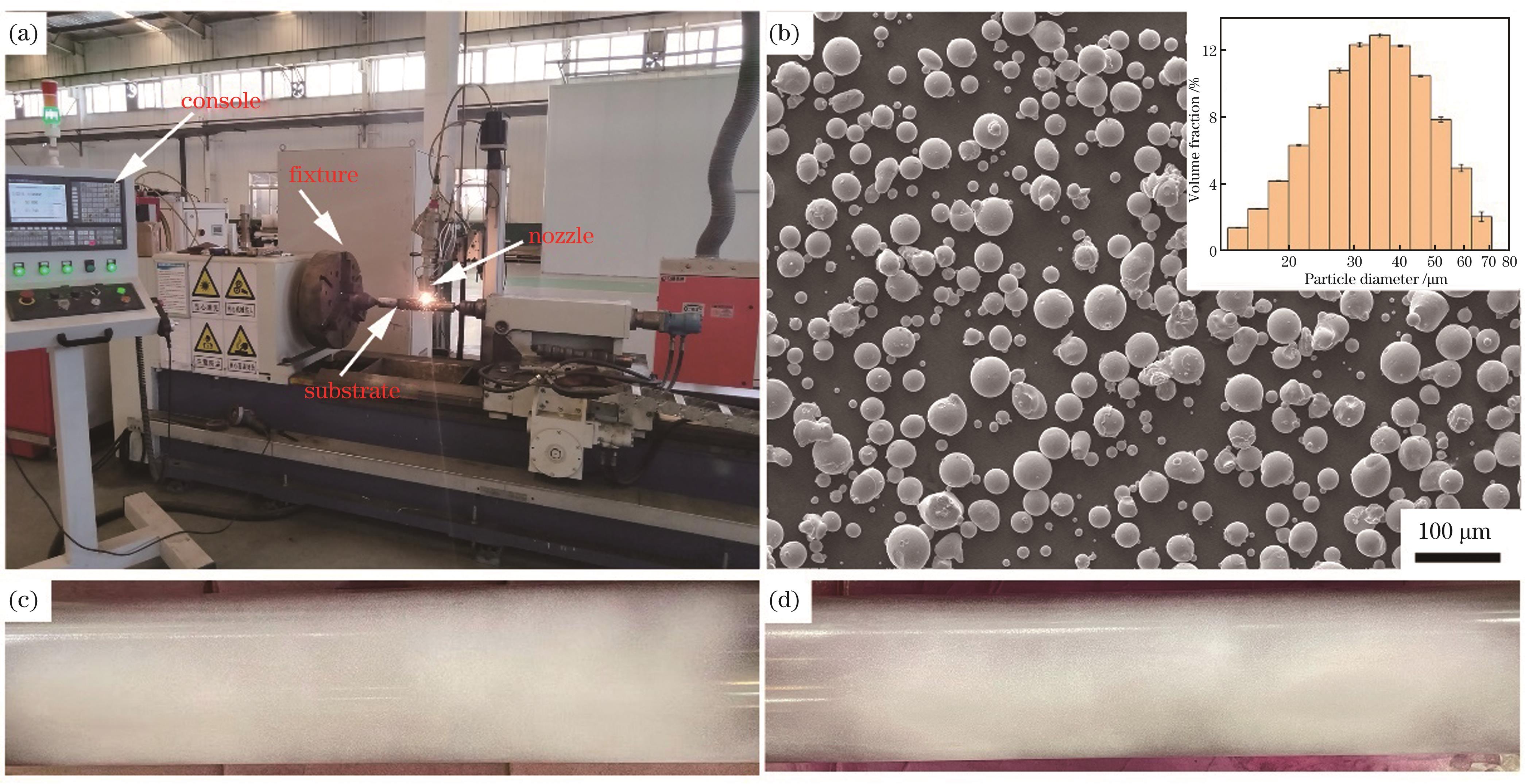
Set citation alerts for the article
Please enter your email address