Jia LI, Qiang CHENG, Xiaokun WANG, Haixiang HU, Longxiang LI, Hongshi LI, Donglin XUE, Xuejun ZHANG. Analysis of the current status of research on accuracy traceability based on computational holographic detection technology(inner cover paper)[J]. Infrared and Laser Engineering, 2024, 53(8): 20240135

Search by keywords or author
- Infrared and Laser Engineering
- Vol. 53, Issue 8, 20240135 (2024)
![(a) Defocused carrier frequency map with center blocking CGH; (b) Skewed carrier frequency map of CGH without central obstruction[4, 6]](/richHtml/irla/2024/53/8/20240135/img_1.jpg)
Fig. 1. (a) Defocused carrier frequency map with center blocking CGH; (b) Skewed carrier frequency map of CGH without central obstruction[4, 6]
![(a) A circular grating scanning electron microscope with a spacing of 1.2 mm written on an 80 nm chromium film; (b) Test images with line spacing of 2, 1.6, 1, 0.8 mm respectively [10]](/richHtml/irla/2024/53/8/20240135/img_2.jpg)
Fig. 2. (a) A circular grating scanning electron microscope with a spacing of 1.2 mm written on an 80 nm chromium film; (b) Test images with line spacing of 2, 1.6, 1, 0.8 mm respectively [10]

Fig. 3. (a) Schematic structure of the hologram for amplitude-type calculation; (b) Schematic structure of the hologram for phase-type calculation

Fig. 4. Schematic diagram of the process of decomposing smooth stripes into polygonal codes

Fig. 5. Kinoform method Fresnel schematic

Fig. 6. Schematic of the numerical representation of the ideal stripe
![CGH production flowchart[24-25]](/Images/icon/loading.gif)

Fig. 8. Analysis of the effect of substrate face shape on wavefront

Fig. 9. Schematic diagram of the positional error of CGH
![(a) Schematic of non-uniform aspherical phase fitting; (b) Schematic of three times B-spline aspherical phase fitting; (c) Schematic of fitted and residual distributions[35]](/Images/icon/loading.gif)
Fig. 10. (a) Schematic of non-uniform aspherical phase fitting; (b) Schematic of three times B-spline aspherical phase fitting; (c) Schematic of fitted and residual distributions[35]

Fig. 11. (a) Graphical calculation of the spherical CGH duty cycle; (b) Theoretically calculated curve of interference fringe contrast versus spherical CGH duty cycle
![(a) Residual wave aberration when a 2% etch depth error is introduced; (b) Residual wave aberration when a 1% duty cycle is introduced[33]](/Images/icon/loading.gif)
Fig. 12. (a) Residual wave aberration when a 2% etch depth error is introduced; (b) Residual wave aberration when a 1% duty cycle is introduced[33]
![Substrate error of CGH detected by interferometry[47]](/Images/icon/loading.gif)
Fig. 13. Substrate error of CGH detected by interferometry[47]
![Schematic of stripe position distortion and beam diffraction at CGH[41]](/Images/icon/loading.gif)
Fig. 14. Schematic of stripe position distortion and beam diffraction at CGH[41]
![Schematic flowchart of accuracy evaluation method system and extraction of contour data points [49]](/Images/icon/loading.gif)
Fig. 15. Schematic flowchart of accuracy evaluation method system and extraction of contour data points [49]

Fig. 16. Schematic of binary linear grating model duty cycle
![(a) Conceptual diagram of DOC produced by BURGE team CAI et al; (b) DOC hardware with LabVIEW user interface[52]](/Images/icon/loading.gif)
Fig. 17. (a) Conceptual diagram of DOC produced by BURGE team CAI et al; (b) DOC hardware with LabVIEW user interface[52]
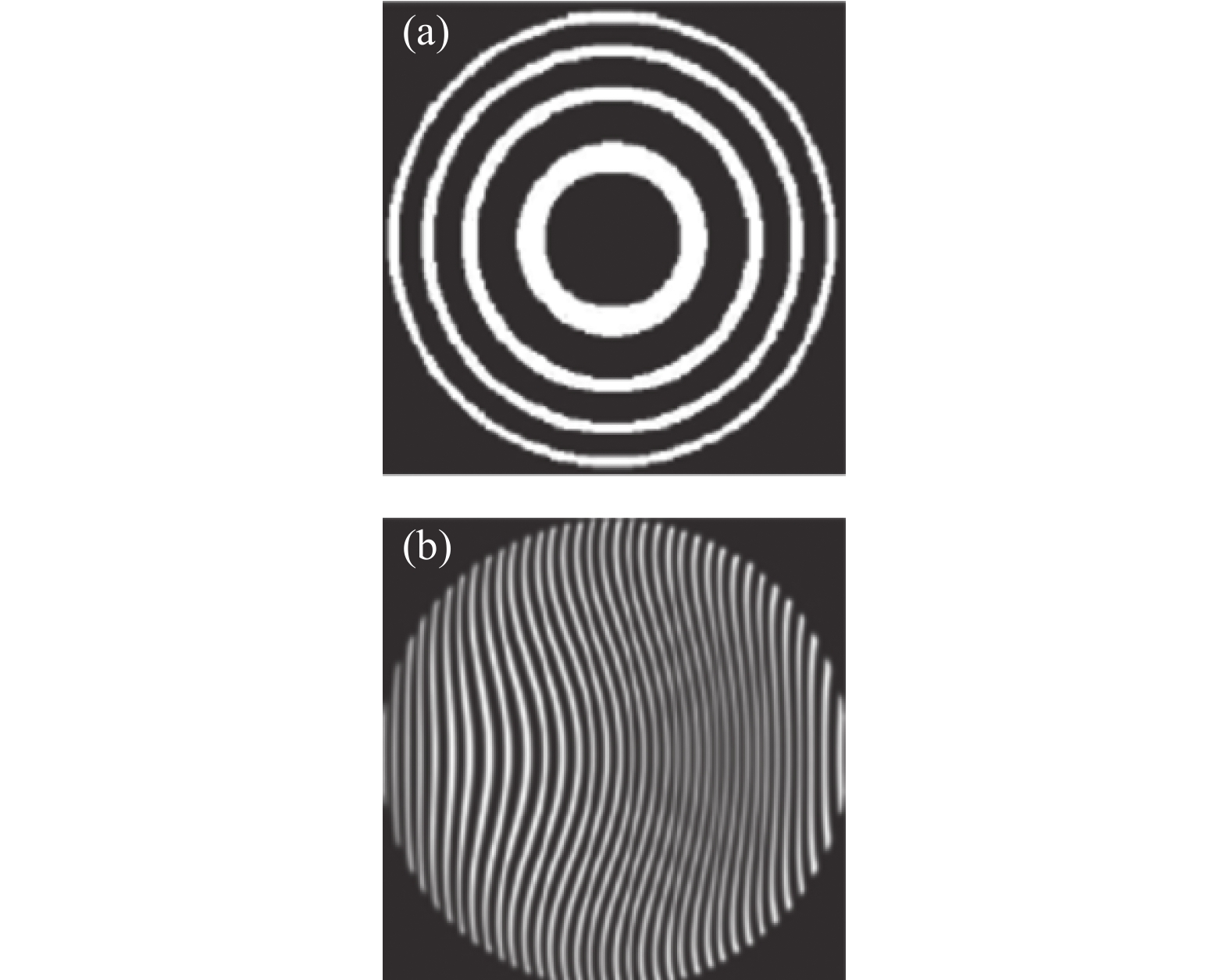
Set citation alerts for the article
Please enter your email address