Geng Zhang, Hua Chen. Simulation and Experimental Study on Laser Scan Cutting Depth of Frozen Ceramic Slurry[J]. Laser & Optoelectronics Progress, 2023, 60(15): 1516003

Search by keywords or author
- Laser & Optoelectronics Progress
- Vol. 60, Issue 15, 1516003 (2023)
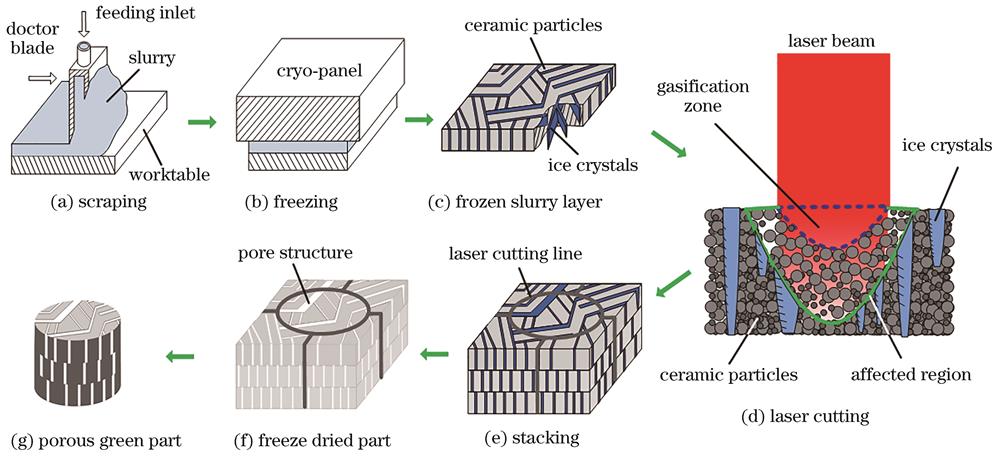
Fig. 1. Machining schematic diagram of FS-LOM
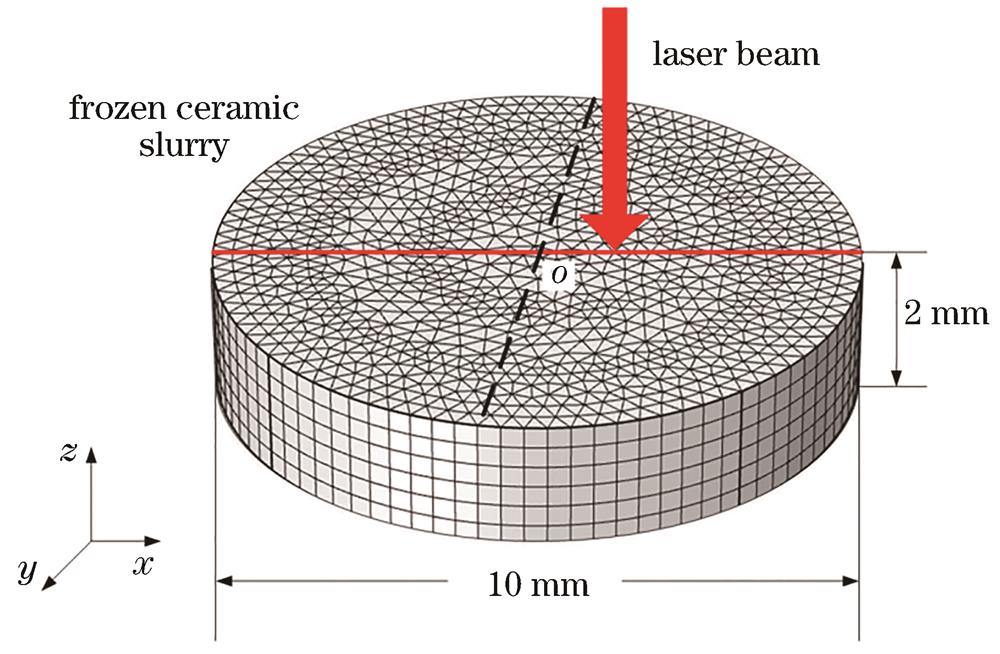
Fig. 2. Material model and mesh generation

Fig. 3. Temperature field distribution of frozen ceramic slurry by laser heating. (a) P=42 W,V=100 mm·s-1,t=0.05 s; (b) P=33 W,V=200 mm·s-1,t=0.25 s; (c) P=33 W,V=100 mm·s-1,t=0.05 s; (d) influence of laser power on temperature field under V=100 mm·s-1; (e) influence of scanning speed on temperature field under P=33 W; (f) influence of laser power and scanning speed on gasification depth

Fig. 4. Theoretical cutting depths of frozen ceramic slurry under different laser powers and scanning speeds

Fig. 5. Experimental results of laser cutting of frozen ceramic slurry. (a) Cross-sectional morphologies of cutting line; (b) comparison between experimental values and simulation values of cutting depth (sim: simulation,exp: experiment)

Fig. 6. Comparison between experimental values and theoretical values of cutting depth (the: theoretical,exp: experimental). (a) Before theoretical model modification; (b) after theoretical model modification

Fig. 7. 3D printing experiment. (a) Ceramic parts processed by FS-LOM; (b) longitudinal porous structure;(c)surface porous structure
|
Table 1. Material ratio of ceramic slurry (mass fraction,%)
|
Table 2. Thermophysical properties of ceramic slurry
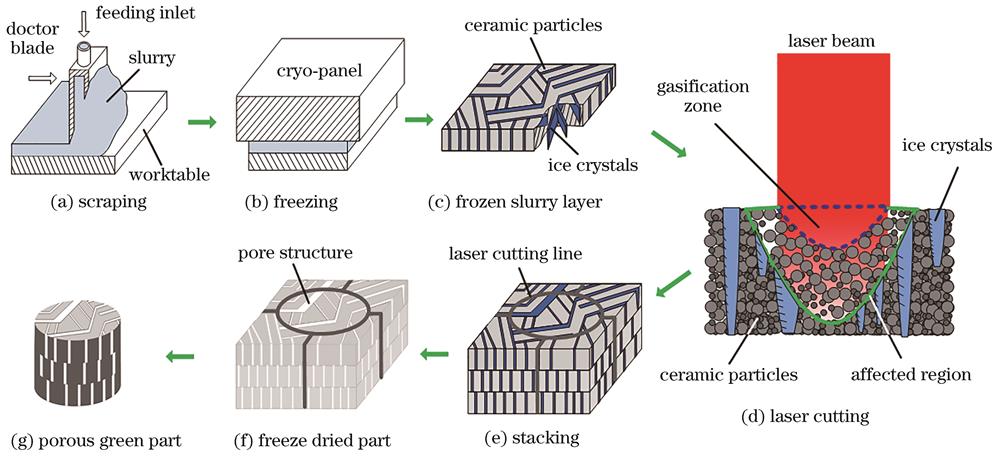
Set citation alerts for the article
Please enter your email address