Zhikai Mi, Fengming Nie, Siling Huang, Feng Xue. Predictive modeling of the surface pattern of double-sided polishing process of optical components[J]. High Power Laser and Particle Beams, 2024, 36(9): 091001

Search by keywords or author
- High Power Laser and Particle Beams
- Vol. 36, Issue 9, 091001 (2024)
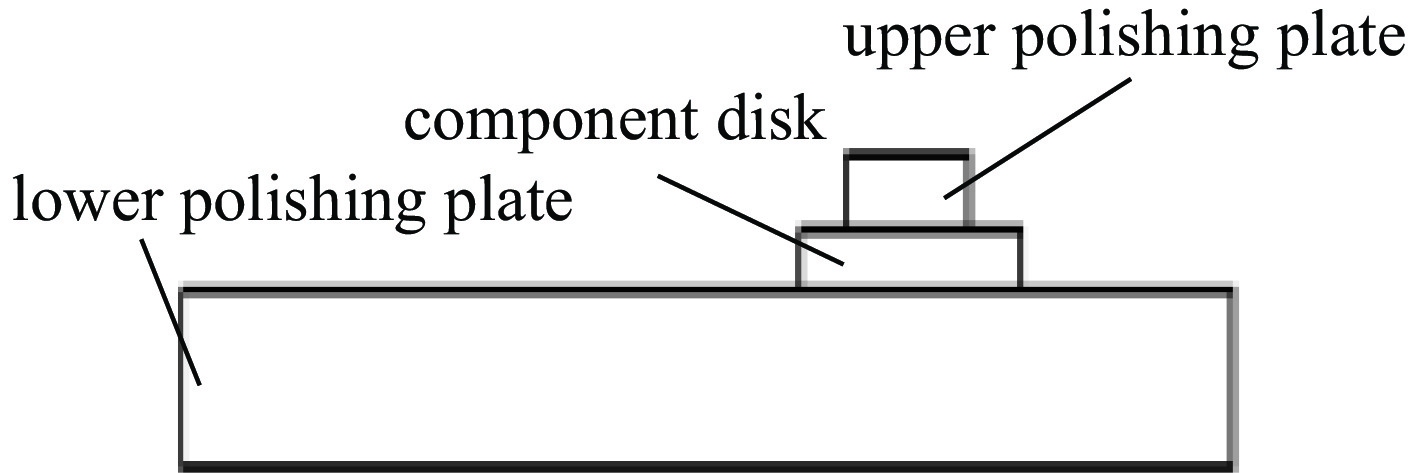
Fig. 1. Sketch of double-sided polishing structure

Fig. 2. Sketch of the relationship between the motion of the down-throwing disc and the element

Fig. 3. Sketch of the relationship between the movement of the up-throwing disc and the element

Fig. 4. Schematic diagram of the position of the upper disk swinging back and forth versus time

Fig. 5. Stress distribution on the lower surface of the upper polishing disk element of 300 mm diameter

Fig. 6. Stress distribution on the lower surface of the component

Fig. 7. Distribution of pressure on the surface of the element at different moments

Fig. 8. Preston coefficient K calculation

Fig. 9. Comparison between the predicted and the experimentally processed surface patterns

Fig. 10. Distribution of prediction and machined surface pattern errors
|
Table 1. Coefficients of pressure distribution equation
|
Table 2. Polishing process parameters in the modified experiment
|
Table 3. Prediction-validated expermental process parameters and comparsion between experimental data predicted data
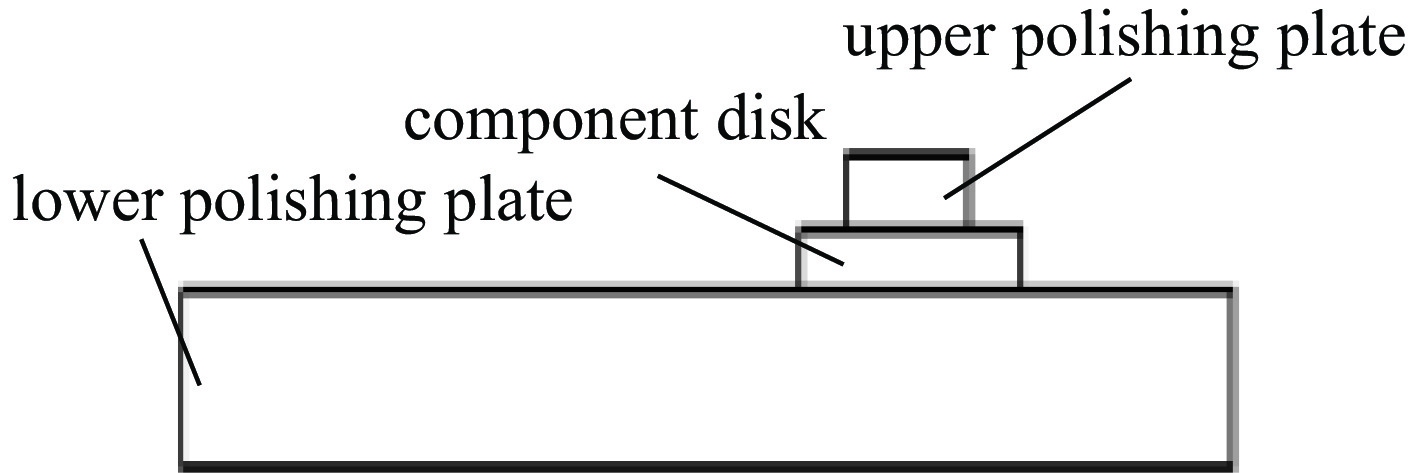
Set citation alerts for the article
Please enter your email address