Xicong Zhu, Rong Chen, Xiansong He, Jin Xie, Shanshan He. Experimental Study on Picosecond Laser Etching and Flow Properties of Glass Microchannels[J]. Chinese Journal of Lasers, 2025, 52(8): 0802404

Search by keywords or author
- Chinese Journal of Lasers
- Vol. 52, Issue 8, 0802404 (2025)
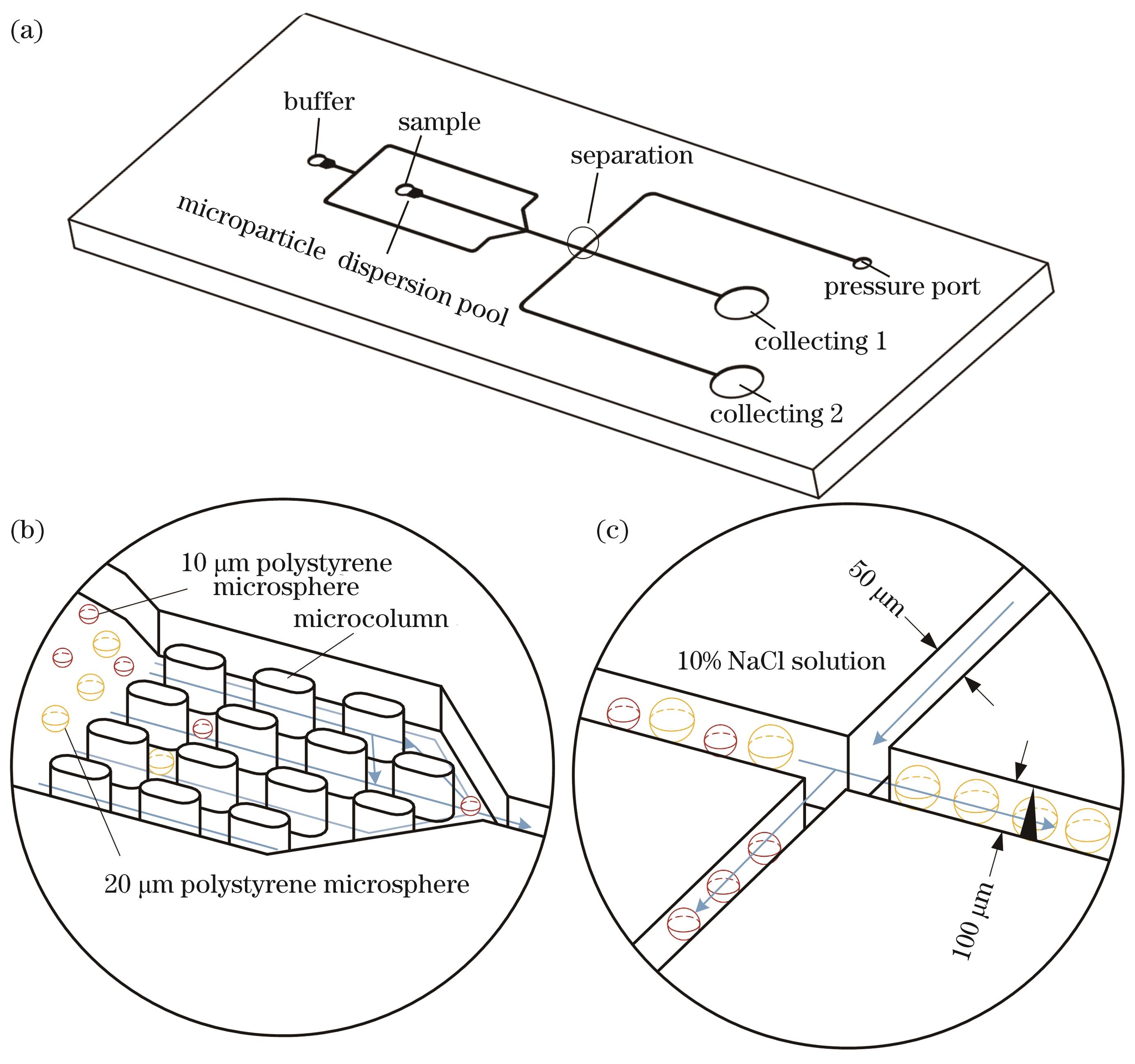
Fig. 1. Design diagrams of micro-nano topology structure of microfluidic chip. (a) Three-dimensional (3D) model of chip;

Fig. 2. Scene of picosecond green light etching of glass

Fig. 3. Schematic diagram of laser optical path

Fig. 4. Laser processing channel path and focus position adjustment. (a) Laser processing roadmap; (b) dynamic adjustment of laser focusing position

Fig. 5. Microfluidic chip packaging scene. (a) Plasma treatment of surface-mounted PDMS materials; (b) laser drilling for PDMS packaging

Fig. 6. Physical picture of encapsulated glass microfluidic chip

Fig. 7. Flow performance testing platform of microfluidic chip

Fig. 8. Relationship between laser power P and microchannel depth h

Fig. 9. Scanning speed vl versus microchannel depth h and surface roughness Ra

Fig. 10. Cumulative number N versus channel depth h and surface roughness Ra

Fig. 11. P, vl, and N versus channel depth h at different levels

Fig. 12. P, vl, and N versus surface roughness Ra at different levels

Fig. 13. 3D morphology detection of microfluidic chips. (a) Micropillar array; (b) crossed microfluidic channels; (c) separation port flow channel

Fig. 14. Fluid detection at array inlet

Fig. 15. Relationship between microsphere speed vs and time t at array inlet

Fig. 16. Flow experimental photos of 45° cross channel processed under different parameters. (a) vl=1000 mm/s, P=15 W, N=6; (b) vl=200 mm/s, P=9 W, N=6

Fig. 17. Detection of microfluidic pinched flow. (a) Pinched flow; (b) microsphere acceleration

Fig. 18. Relationship between microsphere displacement and time t

Fig. 19. Sorting result

Fig. 20. Relationship between microsphere speed vsand time t
|
Table 1. Material characteristics of silica sodium calcium glass
|
Table 2. Process parameters
|
Table 3. Parameter level selection of laser etching channel process
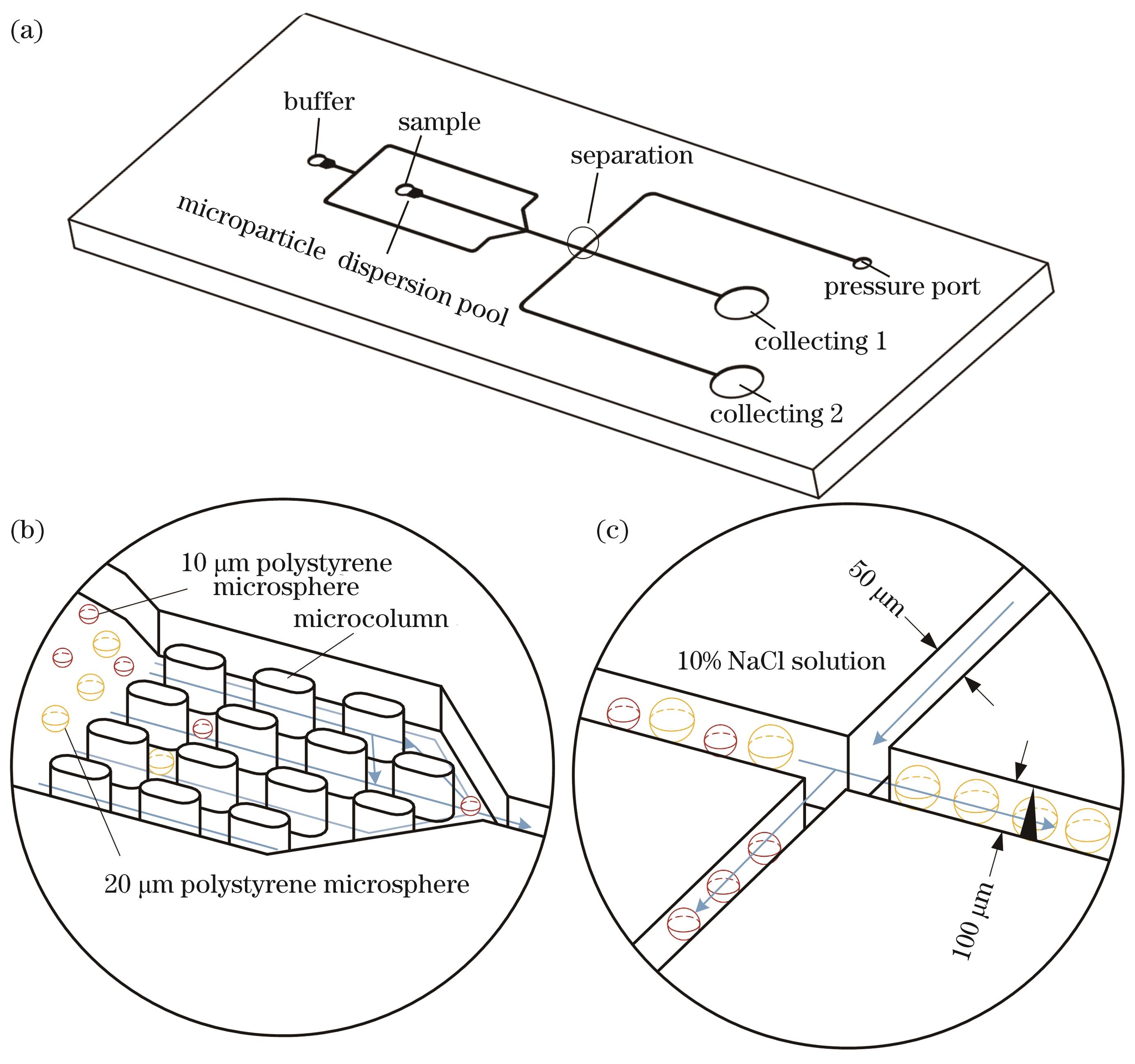
Set citation alerts for the article
Please enter your email address